CYNKOWANIE ELEKTRYCZNE LUB STOPOWE
Metoda cynkowania elektrycznego lub stopowego jest najczęściej stosowaną metodą powlekania części złącznych. Warstwę cienką (3-20 mikronów* dla złączy gwintowanych) cynku lub jego stopu (np. cynk-nikiel, cynk-żelazo) nakłada się na powierzchnię części złącznej z użyciem procesu elektrolitycznego (cynkowania). Następnie, bezpośrednio po pokryciu produktów cynkiem, do stopu cynki-nikiel lub cynk-żelazo dodaje się warstwę pasywacyjną, pełniącą rolę warstwy ochronnej tychże stopów. W cynkowaniu elektrycznym lub stopowym stosuje się szereg warstw pasywacyjnych o różnej barwie i charakterystyce, przeznaczonych dla części złącznych.
*1 mikron (μm) = 0,001 mm.
Proces cynkowania elektrycznego

Jak widać na rysunku powyżej części złączne poddawane cynkowaniu są umieszczone w plastikowym bębnie zanurzonym w zbiorniku wypełnionym elektrolitem (cieczą przewodzącą prąd elektryczny) naładowanym ujemnie (katoda). W zbiorniku umieszczone są naładowane dodatnio pręty z cynku lub z jego stopów (anoda). Podawany do zbiornika prąd służy do przenoszenia jonów cynku lub jego stopów do ujemnie naładowanych złączników stalowych.
Cynk lub stopy cynku są metalami bardziej szlachetnymi od stali. W przypadku zastosowania ich na stali w postaci powłoki ochronnej mogą one pełnić rolę anody dostarczającej elektrony do stali, gdy zacznie ona ulegać korozji w środowisku wilgotnym. Proces taki określa się ochroną katodową.
Miedź, mosiądz, nikiel, chrom, cyna i srebro są również bardziej szlachetne od stali. Zastosowane w formie powłoki ochronnej będą pełniły rolę katody. Dzięki temu możliwe będzie bezpośrednie oddziaływanie na stal, korozja zaś może pojawić się nawet pod powłoką, jeśli wilgoć wejdzie w reakcję ze stalą (anodą) przez pory lub uszkodzenia w strukturze powłoki.
Z tego względu cynk lub jego stopy są metalami najczęściej używanymi do powlekania wyrobów stalowych.
Pasywacja (chromianowanie)
Poziom ochrony antykorozyjnej oferowany przez warstwy cynku lub stopów cynkowych można znacznie zwiększyć w procesie pasywacji. Typowa forma tej dodatkowej obróbki polega na nałożeniu niezwykle cienkiej (ok. 0,1 µm) warstwy chromianu służącej uszczelnieniu porów w warstwie cynku lub jego stopu oraz na związaniu tlenu w warstwie. Warstwa tego typu zawiera chrom 6-wartościowy (Cr(VI)), posiada zatem wyjątkową zdolność "samonaprawiania się". W przypadku uszkodzeń mechanicznych rozpuszczalne sole chromu 6-wartościowego zawarte w warstwie pasywacyjnej "naprawią" (poddadzą powtórnej pasywacji) obszary uszkodzone. Wadą tego procesu jest to, że chrom 6-wartościowy uznano za substancję niebezpieczną, nieprzyjazną środowisku (toksyczną i kancerogenną). Jej używanie w Unii Europejskiej jest ograniczone i coraz częściej zakazywane na mocy różnych dyrektyw (np. RoHS, ELV (patrz odnośniki na końcu dokumentu). Szczegółowe informacje na temat chromianowych powłok konwersyjnych są dostępne w międzynarodowej normie ISO 4520.
W zależności od grubości i składu warstwy pasywacyjnej jej barwa może zmieniać się od przezroczystej (białej), poprzez niebieską, żółtą, do czarnej.
Pasywacja biało-niebieska
Najbardziej rozpowszechniony typ części złącznych oferujący niską ochronę antykorozyjną i w wyniku tego zalecany wyłącznie do stosowania wewnątrz budynku.
Pasywacja czarna
Taki sam poziom ochrony jak w pasywacji biało-niebieskiej i preferowany ze względu na czarny kolor. Zawiera Cr(VI).
Pasywacja żółta
Pasywacja tego typu zapewnia o wiele wyższy poziom odporności na korozję i jest zalecana w aplikacjach zewnętrznych. Negatywny wpływ na jej popularność ma duża zawartość Cr(VI).
Pasywacja zielona (oliwkowa)
Pasywacja zielona ma zastosowanie głównie w branży wojskowej. Poziom odporności na korozję obydwu typów jest porównywalny z poziomem pasywacji żółtej lub wyższy. Powłoki tego typu charakteryzują się również dużą zawartością Cr(VI).
Pasywacja z użyciem chromu 3-wartościowego (Cr(III))
W wyniku dyrektyw dotyczących substancji niebezpiecznych (np. dyrektywy RoHS) konieczne okazało się opracowanie nowej warstwy pasywacyjnej. Warunkiem wstępnym było to, aby zamiast chromu 6-wartościowego warstwa ta zawierała chrom 3-wartościowy (Cr(III)). Niektóre pasywacje tego typu charakteryzują się lepszą odpornością na korozję niż pasywacja Cr(IV). Określa się je często, jako "pasywacje warstwy grubej". Grubość warstwy cienkiej może zawierać się nawet w zakresie 0,08 – 0,1 µm, grubej zaś w zakresie 0,2 - 0,3 µm. Najczęściej stosowaną metodą jest pasywacja warstwy cienkiej. Pasywacje warstwy grubej charakteryzują się szeroką gamą barw (niebieskawo-żółtawo-zielonkawa na warstwach cynkowych, żółtawo-zielonkawa na warstwach ze stopów cynku) i oferują najwyższy poziom odporności na korozję (wyższy od pasywacji żółtej Cr(VI)). Aby jeszcze bardziej zwiększyć poziom odporności i/lub poprawić charakterystykę powłoki można zastosować szczeliwo.
Kruchość wodrowa
Proces cynkowania elektrycznego wykorzystuje elektryczność do wytrącania cynku lub jego stopów. Prąd wywołuje ponadto efekt elektrolizy, w wyniku, której woda zamienia się w wodór i tlen. Tlen zostaje usunięty z cieczy, lecz jony wodoru mogą rozpraszać się w metalach części złącznych i przyczepiać do cząsteczek wodoru. Procesowi temu towarzyszy zwiększenie objętości, co generuje z kolei znaczne naprężenia w strukturze metalu. W połączeniu z zewnętrznymi siłami rozciągającymi może to skutkować opóźnionymi i niezamierzonymi pęknięciami. Trawienie (faza procesu cynkowania ogniowego) bez obecności inhibitorów, a także wykonywane niewłaściwie hartowanie i odpuszczanie stali o wysokich właściwościach mechanicznych może również powodować kruchość materiału pod wpływem wodoru.
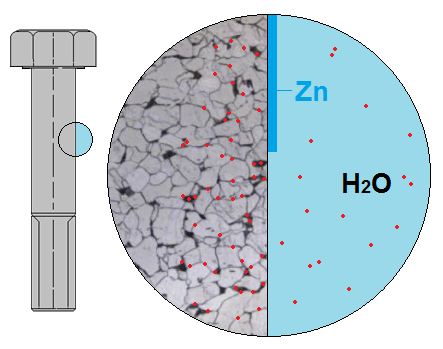

Ryzyko związane z kruchością wodorową dotyczy produktów:
- o sile rozciągającej ≥ 1000 MPa
- o twardości ≥ HV320
- nawęglonych
Aby zminimalizować ryzyko kruchości wodorowej – po procesie cynkowania wymienione wyżej produkty należy poddać powtórnemu rozgrzaniu (wypaleniu) przez odpowiedni okres czasu i w odpowiedniej temperaturze. Międzynarodowa norma dla elektrolitycznych powłok części złącznych (ISO 4042: 1999) stwierdza, między innymi, że części galwanizowane należy poddawać wypalaniu w temp. 200°C do 230° na 4 godziny po galwanizacji i przed chromianowaniem (przy czym czas zalecany to 1h). Należy tu uwzględnić temperaturę maksymalną, materiał powłoki oraz typ materiału bazowego.
Wraz z rosnącą grubością powłoki coraz trudniejsze staje się usuwanie wodoru. Wprowadzenie procesu wypalania pośredniego (dla powłok o grubości 2 - 5 µm) może zmniejszyć ryzyko kruchości wodorowej. Norma ISO 4042 nie określa szczegółowych warunków wypalania. Jednakże, w zależności od typu, rozmiaru, geometrii, właściwości mechanicznych, procesów oczyszczających czy galwanizacyjnych, zastosowanie może mieć czas wypalania w zakresie od 2 do 24h w temperaturze 200°C - 230°C.
W przypadku komponentów o kluczowym znaczeniu zaleca się, aby temperatura i czas były określane eksperymentalnie, przy czym temperatura powtórnego rozgrzewania nie może przekroczyć wartości temperatury odpuszczania. Czas powtórnego rozgrzewania zaczyna się w momencie osiągnięcia temperatury minimalnej przez dane wyroby.
Bez względu na podjęte środki ostrożności bieżące procesy galwanizacji mogą wpływać na redukcję ryzyka kruchości wodorowej, lecz nie mogą go wyeliminować całkowicie. Jeśli nie jest możliwe uwzględnienie żadnego ryzyka w odniesieniu do aplikacji o krytycznym znaczeniu należy wówczas wybrać inny typ powłoki (np. lamele cynkowe).
System kodowania zamówień cynkowania elektrycznego
Zgodnie z normą ISO 4042:1999 galwaniczne powłoki części złącznych są oznaczone kodem składającym się z dwóch wielkich liter i liczby. W przygotowaniu znajduje się nowy system kodowania przeznaczony dla kolejnej wersji normy ISO 4042.
Bieżąca struktura kodu przedstawia się następująco:
- jedna wielka litera dla metalu powłoki - patrz Tabela 1,
- jedna liczba dla minimalnej grubości warstwy (struktura powłoki) – patrz Tabela 2,
- jedna wielka litera dla stopnia połysku i ponownej obróbki – patrz Tabela 3.
Tabelę 1 oparto na normie ISO 4042:1999

Tabelę 2 oparto na normie ISO 4042:1999

Tabelę 3 oparto na normie ISO 4042:1999
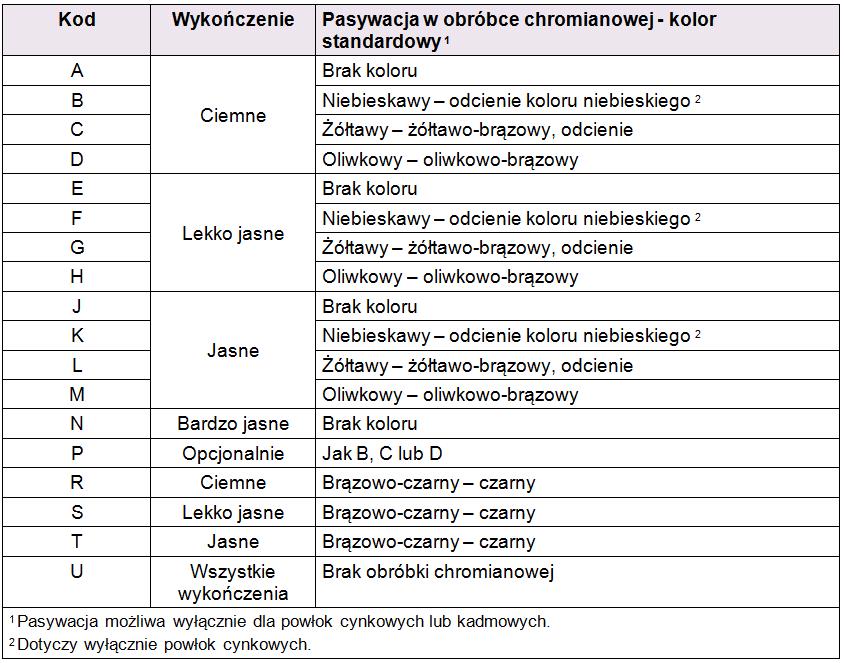
Kod przykładowy: A3L
“A” oznacza cynkowanie (patrz Tabela 1).
“3” oznacza grubość warstwy min. 8 mikronów (patrz Tabela 2).
“L” oznacza pasywację jasno-żółtą (patrz Tabela 3).
Przykładowe oznakowanie: śruba sześciokątna DIN 931 – M16 x 60 – 8.8 – A3L.
W przypadku nieuzgodnienia grubości powłoki zastosowanie ma grubość powłoki dostępna w obrocie handlowym.
Ograniczenia dotyczące grubości powłoki
Stopień ochrony przed korozją jest ogólnie proporcjonalny do grubości zastosowanej warstwy. W przypadku galwanicznych powłok części złącznych grubość nie jest rozprowadzana równomiernie (zależy to, między innymi, od stosunku długości do średnicy – l/d). W przypadku ochrony danego wyrobu charakter normatywny ma grubość warstwy stosowana na poziomie lokalnym. Aby zapobiec korozji śruby / nakrętki podczas montażu maksymalna grubość warstwy nie powinna przekraczać 1/4 wartości dopuszczalnej (patrz rysunek poniżej).

W trójkącie prostokątnym ABC, powłoka AB jest grubością warstwy. Przyrost średnicy podziałowej generowany przez warstwę powłoki wynosi:

W Tabeli 4 przedstawiono maksymalne dopuszczalne grubości warstwy zewnętrznych części złącznych gwintowanych z tolerancją g (przed nałożeniem powłoki) w stosunku do skoku gwintu i długości nominalnej.
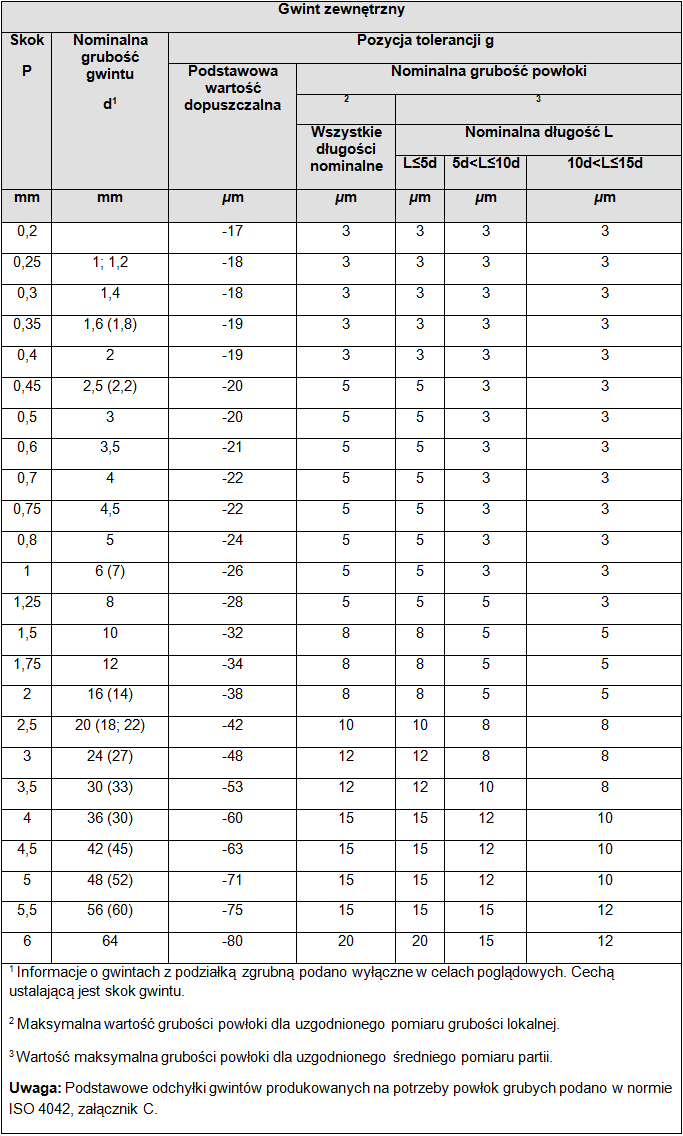
Grubość warstwy - miejsca testowe
Lokalną, minimalną grubość warstwy dla części złącznych należy mierzyć w miejscach przedstawionych na rysunku poniżej.
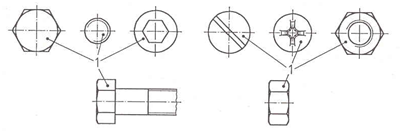
Średnią grubość warstwy danej partii należy ustalać z użyciem metody opisanej w normie ISO 4042, załącznik D. Jeżeli nie ustalono tego inaczej pomiar należy wykonać na poziomie lokalnym.