ZINC OR ZINC ALLOY ELECTROPLATING
This is by far the most common surface coating for steel fasteners. A very thin layer (3 to 20 microns* for threaded fasteners) of zinc or a zinc alloy (e.g., ZnFe, ZnNi) is deposited on the surface of the fastener by an electrolytic (galvanic) process. Directly after the products are covered with zinc, a passivation layer is added to the zinc or zinc alloy layer that serves to protect it. Many different types of passivation layers exist, each with different colors and protective aspects, thus offering various zinc or zinc alloy electroplated fasteners.
*A micron or μm is 0.001 millimeter.
THE ZINC ELECTROPLATING PROCESS

As the above image depicts, the fasteners to be plated are put in a rotating plastic drum, submerged into a tank filled with an electrolyte (conductive fluid) and given a negative charge (cathode). Zinc or zinc alloy bars or sheets are present in the tank and are positively charged (anode). The electrical current transports the zinc or zinc alloy ions to the negatively charged steel fasteners.
Zinc or zinc alloys are less noble than steel. If used as a protective coating on steel, they act as an anode that supplies electrons to the steel if it starts to corrode in a moist environment. This is called cathodic protection.
Copper, brass, nickel, chromium, tin and silver are more noble than steel. If these noble metals are used as a protective coating, they act as a cathode. As a consequence, steel can be directly attacked, and rust may occur even under the coating if moisture comes into contact with the steel (anode) through pores or damage in the coating.
This relationship is why zinc or zinc alloys are the most widely used metals for coating steel products.
PASSIVATION (CHROMATING)
Protection against corrosion offered by the zinc or zinc alloy layers can be improved considerably by passivating the products. In the classical form of this follow-up treatment, an extremely thin chromate layer (approximately 0.1 µm) is formed. This layer seals the pores in the zinc or zinc alloy layer and also binds oxygen to it. It often contains hexavalent chromium, Cr(VI), and therefore possesses a unique ‘self-healing’ property. In case of mechanical damage, the soluble hexavalent chromium salts within the passivation layer repair (re-passivate) the exposed areas. The downside of this post-treatment is that Cr(VI) is considered a hazardous and environmental unfriendly substance as it is toxic and carcinogenic. Its use in the EU is limited and Cr(VI) has been gradually banned by various legislations (e.g., RoHS, ELV). Details about chromate conversion coatings can be found in the international standard lSO 4520.
Depending on the thickness and composition of the passivation layer, the color varies from transparent (white) through blue and yellow to black.
WHITE OR BLUE PASSIVATION
This is the most common type for fasteners. It offers low corrosion protection and is therefore advised for indoor applications.
BLACK PASSIVATION
Black passivation provides the same level of protection as white or blue passivation and is typically chosen for its black color. It contains Cr(VI).
YELLOW PASSIVATION
This type of passivation affords far better corrosion resistance and is commonly advised for outdoor applications; however, it continues to decrease in popularity as the Cr(VI) content is significant.
(OLIVE) GREEN PASSIVATION
These passivation types are mainly for military applications. The corrosion resistance of both types is comparable to or slightly better than yellow passivation, and they also contain Cr(VI).
TRIVALENT CHROMIUM CR(III) PASSIVATION
As a result of hazardous substances legislation, like RoHS, Reach and ELV, a new type of passivation layer without Cr(VI) had to be developed. Instead of Cr(VI), which is present in the black, yellow, brown and green passivation (chromate) layers, most newly developed passivation layers use trivalent chromium, abbreviated as Cr(III). Some of these passivation types even possess better corrosion resistance than Cr(VI) passivation. They are often referred to as ‘thick-layer passivation.’ A thin layer may measure around 0.08 to 0.1 µm, while a thick layer is approximately 0.2 to 0.3 µm. Transparent thin-layer passivation is most commonly used. Thick layer passivation is often iridescent (bluish-yellowish-greenish on zinc layers and yellowish-greenish on zinc alloy layers), and it offers superior corrosion resistance, better than the Cr(VI) yellow passivation. To further improve corrosion resistance and/or enhance the aspect of the coating, a sealant can be applied.
HYDROGEN EMBRITTLEMENT
The electroplating process uses electricity to precipitate zinc or zinc alloys. The current causes also the water to partly electrolyze into hydrogen and oxygen in the bath.
The oxygen disappears from the liquid in the bath, but the hydrogen ions may diffuse into the metal of the fasteners and bind to hydrogen molecules. This process is accompanied by an increase in volume, which causes high stress in the metal structure. In the presence of external tensile forces, such stress can give rise to delayed and spontaneous brittle fractures. Incidentally, hydrogen embrittlement can also be induced by pickling (which is used in the hot dip galvanizing process) without inhibitors and unskilled quenching and tempering of steels with high mechanical properties.
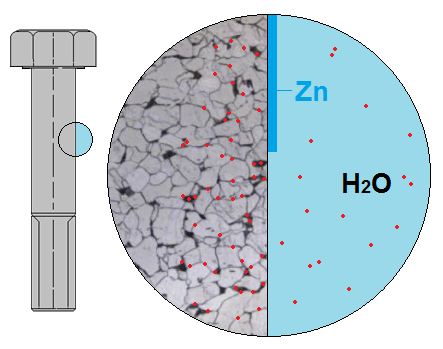

The danger of hydrogen embrittlement applies to products with several characteristics:
- with a tensile strength ≥ 1000 MPa
- with hardness ≥ HV320
- that are case hardened
To minimize the risk of hydrogen embrittlement, these products must be reheated (baked) after the electroplating process for a certain period of time and at a certain temperature. The international standard for electroplated coatings on fasteners, ISO 4042 edition 1999, states that electroplated parts should be baked to a part temperature of 200°C to 230°C within four hours of electroplating, though preferably within one hour, and before chromating. The maximum temperature should be determined with consideration for the coating material and type of base material.
With increasing coating thickness, the difficulty of removing hydrogen increases. However, introduction of an intermediate baking process when the coating is only 2 µm to 5 µm thick may reduce the risk of hydrogen embrittlement.
ISO 4042 does not provide exact baking conditions. Eight hours is considered a typical example of baking duration. However, baking durations between 2 hours and 24 hours between 200°C and 230°C may be suitable depending on the part’s type, size, geometry and mechanical properties, in addition the cleaning and electroplating processes used.
For critical components, it is recommended that the temperature and time be established experimentally, but it is important that the reheating temperature never exceeds the tempering temperature. The reheating time begins as soon as the products have reached the minimum temperature.
Despite all of the care given to the processes, current electroplating techniques can only reduce the danger of hydrogen embrittlement, not eliminate it completely. For critical applications in which risk is unacceptable, another coating method must be chosen (e.g., zinc flake coatings).
CODE SYSTEM FOR ORDERING ZINC ELECTROPLATING
According to ISO 4042:1999, the electroplated coatings of mechanical fasteners are designated by a code that consists of two capitals letters and a number. A new coding system is in preparation for the next edition, ISO 4042.
The current code is structured as follows:
- One capital letter for the coating metal; see table 1
- One capital letter for the coating metal; see table 1
- One capital letter for the degree of gloss and follow-up treatment; see table 3
All tables are based on ISO 4042:1999
TABLE 1
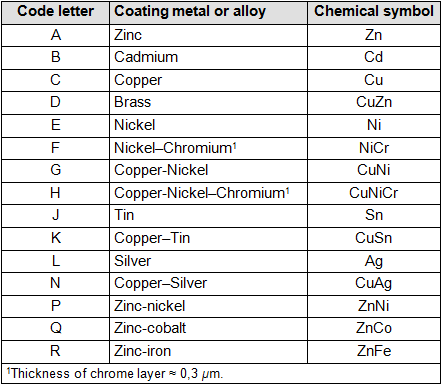
TABLE 2
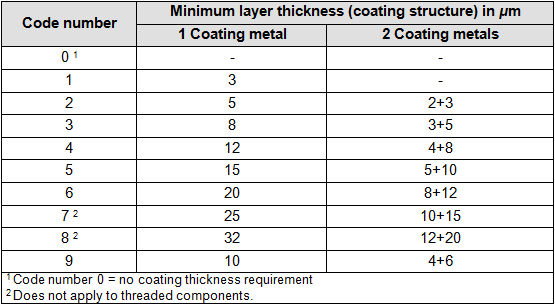
TABLE 3
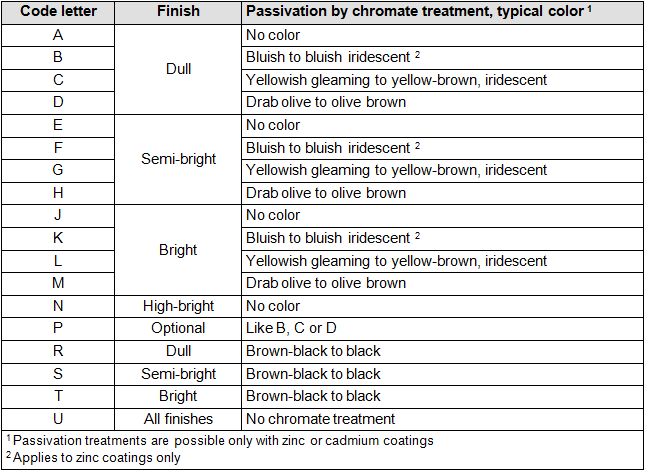
Example of coding: A3L
“A” means zinc plating; see table 1
“3” indicates the layer thickness of at least 8 microns; see table 2
“L” refers to bright yellow passivation; see table 3
Example of designation: hexagon bolt DIN 931 – M16 x 60 – 8.8 – A3L.
If no coating thickness is agreed upon, the commercially available coating thickness is supplied.
LAYER THICKNESS RESTRICTIONS
The degree of protection against corrosion is generally proportional to the thickness of the applied layer. With electroplated coatings on fasteners, however, the thickness is not equally distributed; among other factors, it is dependent on the relationship between length and diameter l/d. For the protection of an article, the minimum local layer thickness is normative. In order to prevent the nut or bolt from seizing during assembly, the maximum nominal layer thickness should not exceed 1/4 of the allowance (see figure below).

In the right-angled triangle ABC, AB is the layer thickness. The increase of the pitch diameter due to the coating layer is denoted by the expression below:

Table 4 shows the maximum permissible layer thicknesses for externally threaded fasteners with tolerance position g (before coating) in relation to the thread pitch and the nominal length.

LAYER THICKNESS TESTING LOCATION
The minimum local layer thickness on fasteners is measured at the points shown in the figure below.
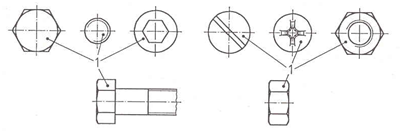
The average layer thickness of a batch must be determined using the method described in ISO 4042, annex D. Unless agreed otherwise, the local layer thickness must be measured.