ACOPERIREA ELECTROLITICĂ CU ZINC SAU CU ALIAJ DE ZINC
Acesta este de departe cea mai utilizată acoperire de suprafață a organelor de asamblare din oțel.Un strat foarte subțire (3 până la 20 microni * pentru elemente de fixare filetate) de zinc sau aliaj de zinc (de exemplu ZnFe, ZnNi) este depus pe suprafața organului de asamblare prin un proces electrolitic (galvanic). Imediat după ce produsele sunt acoperite de zinc, stratul de pasivare este adăugat la stratul de zinc sau aliaj de zinc care servește ca strat de protecție pentru aliajul de zinc sau zinc.Mai multe tipuri de pasivare, cu diferite culori și aspecte de protecție, oferind diferite variante de organe de asamblare cu acoperiri de zinc sau aliaj de zinc.
*Un micron sau μm este de egal cu 0,001 milimetri.
PROCESUL DE ACOPERIRE ELECTROLITICĂ CU ZINC

După cum arată imaginea de mai sus, organele de asamblare care urmează sa fie acoperite sunt așezate într-un tambur de plastic rotativ, scufundat într-un rezervor umplut cu un electrolit (lichid conductiv) și un catod negativ încărcat. Bare sau plăci de zinc sau aliaj de zinc sunt prezente în rezervor și sunt încărcate pozitiv (anod), iar curentul electric va transporta ioni de zinc sau aliaj de zinc la organele de asamblare din oțel încărcate negativ.
Zincul sau aliajele din zinc sunt mai puțin nobile decât oțelul, ca valoare de valență electrolitică. Dacă se utilizează ca o acoperire protectoare pe oțel, acestea acționează ca un anod care furnizează electroni oțelului, dacă începe să corodeze într-un mediu umed. Acest fenomen se numește protecție catodică.
Cuprul, alama, nichelul, cromul, staniul și argintul sunt mai nobile decât oțelul, ca valoare de valență electrolitică. Dacă aceste metale nobile sunt folosite ca strat de protecție, ele acționează ca un catod. Ca o consecință, oțelul poate fi atacat direct, iar rugina poate apărea chiar sub acoperire dacă umezeala intră în contact cu oțelul (anodul) prin pori în stratul de acoperire (sau ca urmarea a deteriorării acestuia).
Acesta este motivul pentru care zincul sau aliajele de zinc sunt cele mai utilizate metale de acoperire pentru produsele din oțel.
PASIVAREA (CROMAREA)
Protecția împotriva coroziunii oferită de straturile de zinc sau aliaj de zinc poate fi îmbunătățită considerabil prin pasivarea produselor. În forma clasică a acestui tratament ulterior se formează un strat de cromat extrem de subțire (cca 0,1 μm) care sigilează porii din stratul de zinc sau aliaj de zinc și, de asemenea, leaga oxigenul de acesta. Acest strat adesea conține crom hexavalent (Cr (VI)) si de aceea poseda o proprietate unică denumită auto-vindecare. In caz de deteriorare mecanica, hexavalentul solubil Crom (VI) este considerat o substanță periculoasă, periculoasă pentru mediu (toxică și carcinogenă). Utilizarea sa în UE este limitată și Cr (VI) a fost treptat interzis de diferite legislații (de exemplu, RoHS, ELV - vezi link-urile de la sfârșitul acestui document.) Detalii despre acoperirile de conversie cu cromat se regăsesc în standardul internațional ISO 4520.
În funcție de grosimea și compoziția stratului de pasivare, culoarea variază de la transparent (alb) până la albastru și galben până la negru.
PASIVAREA ALBĂ/ALBASTRĂ
Acesta este cel mai comun tip de pasivare pentru organele de asamblare, oferind o protecție redusă împotriva coroziunii și, prin urmare, recomandat pentru aplicațiile de interior.
PASIVAREA NEAGRĂ
Același nivel de protecție ca pasivarea albă / albastră și ales de cele mai multe ori pentru culoarea sa neagră. Conține Cr (VI).
PASIVAREA GALBENĂ
Acest tip de pasivare oferă o rezistență la coroziune mult mai bună și este frecvent recomandat pentru aplicații în aer liber, totuși aceasta scade în popularitate, deoarece conținutul de Cr (VI) este semnificativ.
PASIVAREA VERDE
Aceste tipuri de pasivare sunt în principal destinate aplicațiilor militare. Rezistența la coroziune a ambelor tipuri este comparabilă sau ușor mai bună decât pasivarea galbenă și conține, de asemenea, Cr (VI).
PASIVARE CU CROM TRIVALENT (CR(III))
Ca urmare a legislației privind substanțele periculoase, cum ar fi RoHS, Reach și ELV, a trebuit să se dezvolte un nou tip de strat de pasivare. Acest nou strat de pasivare nu mai trebuie să conțină Cr (VI). În loc de Cr (VI), prezente în straturile de pasivare (negru, galben, maro și verde), cele mai multe pasivări recent dezvoltate utilizează crom trivalent (Cr (III)). Unele dintre aceste pasivări au chiar o rezistență mai bună la coroziune decât pasivarea cu Cr (VI). Acestea sunt adesea denumite "pasivarea cu straturi groase". Un strat subțire poate avea grosimea de la 0,08 până la 0,1 μm, iar un strat gros poate măsura de la 0,2 până la 0,3 μm. Se utilizează cel mai frecvent o pasivare transparentă. Pasivările cu straturi groase sunt irizante (alb-gălbui-verzuie pe straturi de zinc, galben-verzuie pe straturi de aliaje de zinc) și oferă o rezistență superioară la coroziune, mai bună decât pasivarea galbenă Cr (VI). Pentru a îmbunătăți în continuare rezistența la coroziune și / sau pentru a spori aspectul stratului de acoperire, poate fi aplicat un agent de etanșare.
FRAGILIZAREA LA HIDROGEN
Procesul de galvanizare folosește energia electrică pentru precipitarea zincului sau a aliajelor de zinc. Cauzele actuale, de asemenea, de a electroliza apa din baie parțial în hidrogen și oxigen.
Oxigenul dispare din lichidul din baie, dar ionii de hidrogen pot difuza în metalul elementelor de fixare și se leagă în molecule de hidrogen. Acest lucru este însoțit de o creștere a volumului, care provoacă presiuni mari în structura metalică. În prezența forțelor externe de tracțiune, aceastea pot genera fracturi întârziate, spontan. De altfel, decaparea fără inhibitori (decaparea așa cum este utilizată în
procedeul de galvanizare la cald) și răcirea și temperarea necalificate a oțelurilor cu proprietăți mecanice ridicate pot, de asemenea, să inducă fragilizarea la hidrogen.
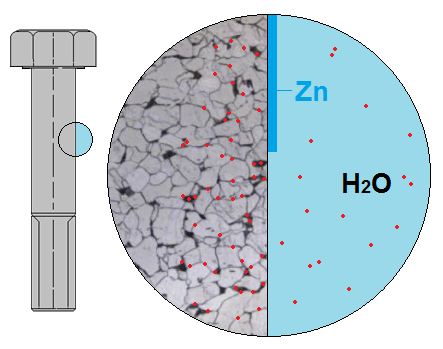

Pericolul fragilizării la hidrogen se aplică produselor:
- cu o rezistență la tracțiune ≥ 1000 MPa
- cu duritate ≥ HV320
- care sunt călite
Pentru a reduce la minimum riscul de fragilizare la hidrogen aceste produse trebuie reîncălzite (coapte) după procesul de galvanizare pentru o anumită perioadă de timp și la o anumită temperatură. Standardul internațional pentru acoperirile electrolitice pe elemente de fixare, ISO 4042, ediția 1999, prevede (printre altele) ca piesele electrolitice să fie coapte timp de 4 ore, dar de preferință la o oră de la galvanizare și înainte de cromare, la o temperatură parțială de 200 ° C 230 ° C. Temperatura maximă trebuie să țină cont de materialul de acoperire și de tipul materialului de bază.
Cu creșterea grosimii stratului de acoperire, dificultatea de eliminare a hidrogenului crește. Introducerea unui proces intermediar de coacere atunci când stratul de acoperire este de numai 2 μm până la 5 μm grosime poate reduce riscul de fragilitate la hidrogen.
ISO 4042 nu oferă condiții exacte de coacere. Opt ore sunt considerate un exemplu tipic de durată de coacere. Cu toate acestea, duratele de coacere în intervalul de la 2h la 24h la 200 ° C până la 230 ° C pot fi potrivite în funcție de tipul și mărimea piesei, geometria părții, proprietățile mecanice, procesele de curățare și procedeele de galvanizare utilizate.
Pentru componentele critice, se recomandă ca temperatura și timpul să fie stabilite experimental, cu toate acestea, temperatura de reîncălzire nu trebuie să depășească niciodată temperatura de temperare. Timpul de reîncălzire începe imediat ce produsele au atins temperatura minimă.
În ciuda tuturor precauțiilor luate, procesele actuale de galvanizare pot reduce riscul de fragilizare a hidrogenului, dar nu pot exclude complet acest fenomen. Dacă nu se pot elimina toate riscurile pentru aplicațiile critice, trebuie aleasă o altă metodă de acoperire (de exemplu, acoperirrea cu fulgi de zinc).
SISTEMUL DE CODIFICARE PENTRU COMANDAREA ARTICOLELOR ZINCATE ELECTROLITIC
În conformitate cu ISO 4042: 1999, acoperirile electrolitice ale organelor de asamblare sunt desemnate printr-un cod format din două majuscule și un număr. Se pregătește un nou sistem de codificare pentru următoarea ediție ISO 4042.
Codul curent este construit după cum urmează:
- O literă majusculă pentru acoperirea metalului, vezi tabelul 1
- Un număr pentru grosimea minimă a stratului (structura de acoperire), vezi tabelul 2
- O literă majusculă pentru gradul de luciu și tratamentul ulterior, vezi tabelul 3
Toate tabelele se bazează pe ISO 4042: 1999
TABELUL 1
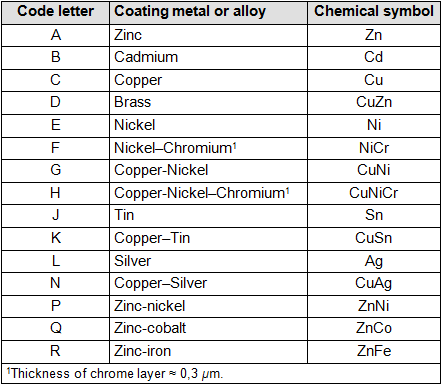
TABELUL 2
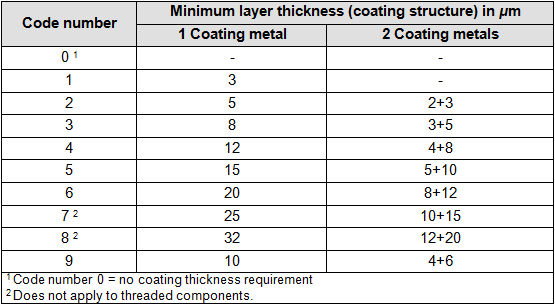
TABELUL 3
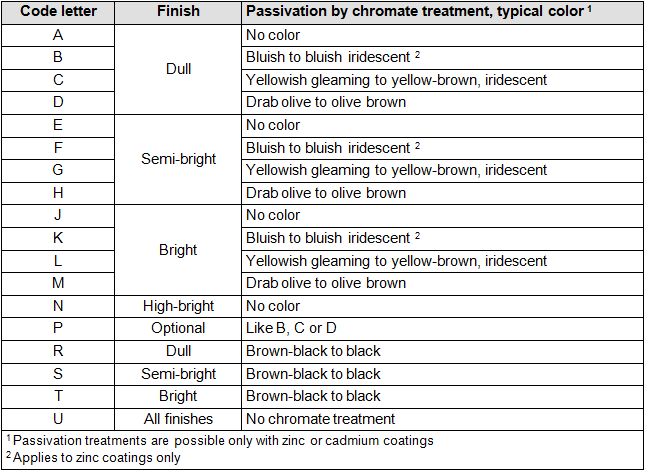
Exemplu de codificare: A3L
"A" înseamnă zincare electrolitică (vezi tabelul 1)
"3" indică grosimea stratului de cel puțin 8 microni (a se vedea tabelul 2)
"L" se referă la o pasivare galben deschis (vezi tabelul 3)
Exemplu de desemnare: Șurub hexagonal DIN 931 - M16 x 60 - 8,8 - A3L.
Dacă nu se solicită o grosime anume a stratului de acoperire, este furnizată grosimea de acoperire disponibilă în comerț.
RESTRICȚII LEGATE DE GROSIMEA STRATULUI DE ACOPERIRE
Gradul de protecție împotriva coroziunii este, în general, proporțional cu grosimea stratului aplicat. Cu toate acestea, grosimea nu este distribuită în mod egal (în funcție de relația dintre lungime și diametru l / d). Pentru protecția unui articol, grosimea minimă a stratului local este normativă. Pentru a preveni griparea piuliței / șurubului în timpul asamblării, grosimea maximă nominală a stratului nu trebuie să depășească 1/4 din cota de permisiune (a se vedea figura de mai jos).

În triunghiul drept ABC, AB este grosimea stratului. Creșterea diametrului de pas datorat stratului de acoperire este:

Tabelul 4 prezintă grosimea maximă a straturilor admisibile pentru organele de asamblare cu filet exterior cu poziția de toleranță g (înainte de acoperire), în raport cu pasul filetului și lungimea nominală.

ZONA DE TESTARE A GROSIMII STRATULUI DE ACOPERIRE
Grosimea minimă a stratului local pe dispozitive de fixare se măsoară în punctele prezentate în figura de mai jos.
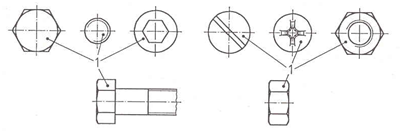
Grosimea medie a stratului unui lot trebuie determinată utilizând metoda descrisă în ISO 4042, anexa D. Dacă nu se convine altfel, trebuie măsurată grosimea stratului local.