ELEKTROMOS VAGY CINKES HORGANYZÁS
Az acél kötőelemek esetében messze ez a legelterjedtebb felületkezelés. Elektrolitos (galván) eljárással egy nagyon vékony (menetes kötőelemek esetében 3-tól 20 mikronig terjedő) cink vagy cinkötvözetből (pl. ZnFe, ZnNi) álló réteggel vonják be a kötőelem felületét. Rögtön azt követően, hogy a termékeket cinkkel vonják be, a cink vagy cinkötvözetből álló réteghez még egy passzivált réteget is adnak, ami védi a cinket vagy a cinkötvözetet. Számos különféle passzivált réteg létezik, különféle színekben és eltérő védelmi tulajdonságokkal, amiket az elektromosan vagy cinkkel horganyzott kötőelemekhez kínálnak.
*Egy micron vagy μm egyenlő 0,001 milliméterrel.
Az elektromos horganyzás eljárása

Amint az a fenti ábrán látható, a horganyzásra kerülő kötőelemeket beleteszik egy forgó műanyag hordóba, amit belemerítenek egy elektrolittal (elektromosan vezető folyadékkal) teli és negatív töltésű (katódos) tartóedénybe. Cinkből, vagy cinkötvözetből készült rudak vagy lemezek is vannak a tartóedényben, amelyek pozitív töltésűek (anód), az elektromos áram pedig a cink vagy cinkötvözet ionokat a negatív töltésű acél kötőelemekre viszi.
A cink vagy a cink ötvözet kevésbé nemes, mint az acél. Ha védőrétegként alkalmazzák acél felületen, akkor úgy viselkedik, mint egy anód, ami elektronokat ad át az acélnak, ha az nedves környezetben elkezd korrodálódni. Ezt nevezik katódos védelemnek.
A vörös-, a sárgaréz, a nikkel, a króm, az ón és az ezüst nemesebbek, mint az acél. Ha ezeket a nemes fémeket védő bevonatként használják, akkor katódként viselkednek. Ennek következtében az acél közvetlenül támadható less és rozsda jelenhet meg még a bevonat alatt is, ha a nedvesség kapcsolatba kerül az acéllal (az anóddal) a bevonat pórusain vagy sérülésein keresztül.
Ezért az acéltermékek esetében a cink vagy a cink ötvözetek a legelterjedtebb felületkezelő fémek.
Passziválás (krómozás)
A termékek passziválásával jelentősen javíthatjuk a cink- vagy cinkötvözet rétege által nyújtott korrózió elleni védelem hatékonyságát. Ennek az utókezelésnek a klasszikus formájában egy rendkívül vékony (kb. 0,1 µm) króm réteg képződik, ami lezárja a pórusokat a cinkből vagy cinkötvözetből álló rétegben és oxigént is köt hozzá. Ez a réteg gyakran tartalmaz hat vegyértékű krómot (Cr(VI)) és ezáltal egyedi “öngyógyító” tulajdonsággal bír. Mechanikai sérülés esetén az oldódó hatvegyértékű krómsók a passzivált rétegen belül “megjavítják” (újrapassziválják) a sérült felületet. Ennek az utókezelésnek az árnyoldala, hogy a Cr(VI)-ot egészségre káros, környezetszennyező anyagnak (mérgező és rákkeltő) tekintik. Használatát az EU-n belül korlátozták és különböző rendeletekkel (pl. RoHS, ELV (a linkeket lásd a dokumentum végén)) a Cr (VI)-ot fokozatosan betiltották. A krómot felváltó felületkezelésekről további információk találhatók az ISO 4520 nemzetközi szabványban.
A passzivált réteg vastagságától és összetételétől függően színe az átlátszótól (fehér) a kéken és a sárgán át a feketéig terjed.
Fehér/kék passziválás
Ez a legelterjedtebb típus a kötőelemeknél, alacsony hatékonyságú korrózió elleni védelmet nyújt, azért beltéri alkalmazásokra ajánlják.
Fekete passziválás
A korrózió elleni védelme ugyanolyan hatékony, mint a fehér/kék passziválásé, főként a fekete színe miatt választják. Cr(VI)-ot tartalmaz.
Sárga passziválás
Ez a típusú passziválás sokkal jobb korrózió elleni védelmet biztosít és általában ezt ajánlják kültéri alkalmazások esetében, habár népszerűsége csökken, mivel jelentős a Cr(VI) tartalma.
(Oliva) zöld passziválás
A passziválásnak ezek a típusai főként katonai alkalmazásokhoz készülnek. Mindkét típus korrózió elleni tulajdonságai felérnek a sárga passziváláséval, vagy kissé meg is haladják azt és ezek is tartalmaznak Cr(VI)-ot.
Három vegyértékű króm (Cr(III)) passziválás
A káros anyagokra vonatkozó rendelkezések – mint például a RoHS, Reach és az ELV – eredményeként egy új típusú passzivált réteget kellett kifejleszteni. Ez az új passzivált réteg már nem tartalmazhat Cr(VI)-ot. A fekete, sárga, barna és zöld passzivált (krómozott)rétegekben jelen lévő Cr(VI) helyett a legtöbb újonnan kifejlesztett passziválási eljárás három vegyértékű krómot (Cr(III)) használ. Némelyik ezek közül a passziválások közül még jobb korrózióálló tulajdonságokkal rendelkezik, mint a Cr(VI) passziválás. Gyakran “vastag rétegű passziválás”-nak is nevezik őket. Egy vékony réteg akár 0,08 - 0,1 µm vastagságú is lehet, egy vastag réteg pedig 0,2 - 0,3 µm. Leggyakrabban egy vékony réteg átlátszó passziválást használnak. A vastag rétegű passziválások több színben játszanak (kékes-sárgás-zöldes a cink bevonaton, sárgás-zöldes a cink ötvözeteken) és rendkívül jó korrózióálló tulajdonságokkal rendelkeznek, jobbal, mint a Cr(VI)sárga passziválás. A korrózió elleni védelem további javítására és/vagy a felületkezelés erősítésére tömítőanyagot is alkalmazhatunk.
Hidrogénes elridegedés
Az elektromos horganyzás elektromosságot használ a cink vagy a cinkötvözet felviteléhez. Az áram elektrolízis révén a fürdőben lévő vizet részben hidrogénre és oxigénre bontja.
Az oxigén eltűnik a fürdőben lévő folyadékból, de a hidrogén ionok bediffundálhatnak a kötőelem fémjébe és a hidrogén molekulákhoz kötődhetnek. Ez térfogat növekedéssel jár, ami feszültséget kelt a fém szerkezetében. Amennyiben külső feszítő erők hatnak rá, ez késleltetett, spontán rideg törést eredményezhet. Alkalomadtán a gátlóanyag nélküli pácolás (a tűzihorganyzás eljárásánál alkalmazotthoz hasonló pácolás) és a magas mechanikai jellemzőkkel rendelkező acélok nem szakszerű megeresztése is előidézheti a hidrogénes elridegedést.
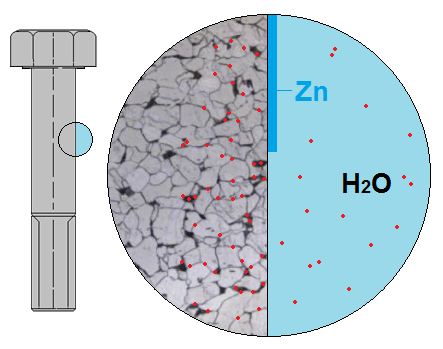

A hidrogénes elridegedés veszélye a következő termékeknél áll fenn:
- szakítószilárdságuk ≥ 1000 MPa
- keménységük ≥ HV320
- mintában edzetteknél
Azért, hogy minimálisra csökkentsük a hidrogénes elridegedés kockázatát ezeket a termékeket az elektromos horganyzás után adott hőmérsékleten újra kell hevíteni (kégetni) egy adott ideig. Az elektromosan horganyzott kötőelemekre vonatkozó nemzetközi szabvány - az ISO 4042 1999-es kiadása – (egyebek mellett) azt állítja, hogy az elektromosan horganyzott eszközöket az elektromos horganyzást követően 4 órán – de lehetőleg egy órán belül - kell kiégetni, még a krómozás előtt úgy, hogy az eszköz hőmérséklete 200°C - 230°C legyen. A maximális hőmérsékletnél figyelembe kell venni a bevonó anyagot és az alapanyag típusát.
Minél vastagabb a bevonat, annál nehezebb eltávolítani a hidrogént. Egy köztes kiégetési eljárás bevezetése, amikor a bevonat még csak 2 µm - 5 µm vastag, csökkentheti a hidrogénes elridegedés veszélyét.
Az ISO 4042 nem írja le a kiégetés pontos feltételeit. Általában egy kiégetés nyolc óráig tart. Azonban az eszköz méretétől és típusától, geometriájától, mechanikai tulajdonságaitól, a tisztító eljárásoktól és az elektromos horganyzási eljárásoktól függően a kiégetés tartama 2-től 24 óráig is eltarthat 200°C-tól 230°C-ig.
Kritikus komponenseknél ajánlatos kikísérletezni a hőmérsékletet és az időt, azonban az újrahevítés hőmérséklete soha nem haladhatja meg az edzés hőmérsékletét. Az újrahevítés ideje onnantól számítódik, amikor a termék elérte a minimális hőmérskletet.
Azonban minden elővigyázatosság ellenére, a jelenlegi elektromos horganyzási eljárások ugyan csökkentik a hidrogénes elridegedés veszélyét, de nem tudják azt teljesen kiküszöbölni. Kritikus alkalmazásoknál, ahol semmilyen kockázat nem megengedhető, más felületkezelési eljárást kell választani (pl. cink pelyhes felületkezelést).
Kódrendszer elektromos horganyzás megrendeléséhez
Az ISO 4042:1999 szerint a mechanikus kötőelemek elektromos horganyzásának jelölésére egy kódrendszert használnak, ami két naygbetűből és egy számból áll. Már készül az új kódrendszer az ISO 4042 következő kiadásához.
A jelenlegi kód a következőképpen áll össze:
- Egy nagy betű a bevonó fémre, lásd az 1. táblázatot
- Egy szám jelöli a minimális rétegvastagságot (bevonat szerkezete), lásd a 2. táblázatot
- Egy nagy betű a fényességi fokozat és az utókezelés meghatározására, lásd a 3. táblázatot
Táblázatot 1 azon alapszik ISO 4042:1999

Táblázatot 2 azon alapszik ISO 4042:1999

Táblázatot 3 azon alapszik ISO 4042:1999
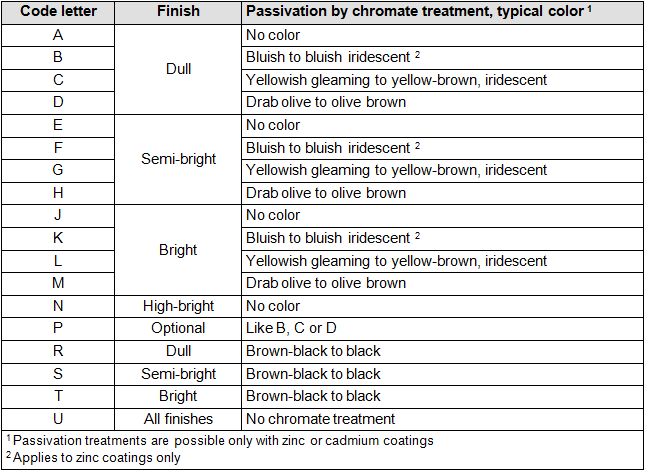
Példa a kódolásra: A3L
“A” jelzi a cink horganyzást (lásd 1. táblázat)
“3” azt jelenti, hogy a rétegvastagság legalább 8 mikron (lásd 2. táblázat)
“L” ragyogó sárga passziválásra utal (lásd 3. táblázat)
Példa a jelölésre: hatlapos csavar DIN 931 – M16 x 60 – 8.8 – A3L.
Ha nem szerepel az egyezségben a rétegvastagság, akkor a kereskedelmileg elérhető bevonati rétegvastagságot kell nyújtani.
A rétegvastagság korlátozásai
A korrózió elleni védelem foka általában arányos a felvitt réteg vastagságával. Azonban az elektromos horganyzású bevonatok a kötőelemek esetében nem egyenletes vastagságban oszlanak el (ez egyebek mellett függ a hossztól és az átmérőtől is l/d). A termékek védelmére az adott helyen meglévő minimális rétegvastagságot normalizálták. Azért, hogy az összeszerelés során az anya/csavar berágódását meggátolják, a maximális névleges rétegvastagság nem lépheti túl a tűrésmező ¼-ét (lásd az alábbi ábrán).

Az ABC derékszögű háromszögben AB a rétegvastagság. A menetemelkedés átmérője a bevonó réteg miatt a következőképpen növekszik:

A 4. táblázat a külső menetes kötőelemeknél maximálisan megengedhető rétegvastagságokat mutatja g tolerancia pozícióval (horganyzás előtti), a menetemelkedéshez és a névleges hosszhoz viszonyítva.

A rétegvastagság tesztelési pontjai
A minimális helyi rétegvastagságot a kötőelemeken az alábbi ábrán látható pontokon mérik.
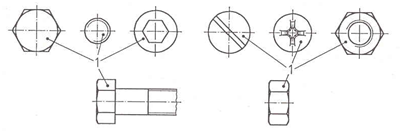
Egy sorozat átlagos rétegvastagságát az ISO 4042 D függelékében meghatározott módszer szerint kell meghatározni. Hacsak külön másként nem egyeznek meg, a helyi rétegvastagságot meg kell mérni.