ELECTRO ZINCAGEM OU ZINCADO
Este é de longe o tratamento de superfície mais comum para artigos de fixação em aço. Uma camada muito fina (3 a 20 microns* para artigos roscados) de zinco ou uma liga de zinco (ex. ZnFe, ZnNi) é depositada na superfície do artigo de fixação por um processo electro lítico (galvânico). Diretamente após os produtos serem cobertos com zinco, uma camada de passivação é feita no zinco – ou na liga de zinco, que serve como proteção para o zinco ou liga de zinco. Existem muitos tipos diferentes de passivação, com cores e proteção diferentes, oferecendo vários elementos de fixação electro zincados ou com liga de zinco.
*um micron ou μm é 0,001 milímetro.
O processo de electro zincagem

Como mostra a imagem acima, os artigos de fixação são colocados num tambor rotativo de plástico, submergido num tanque cheio com um eletrólito (fluido condutor) e carregado negativamente (cátodo). Barras ou folhas de Zinco- ou Liga de zinco estão presentes no tanque e são carregadas positivamente (ânodo), e a corrente elétrica transportará os iões de zinco ou liga de zinco para os artigos de fixação carregados negativamente.
O zinco ou as ligas de zinco são menos nobres que o aço. Se usado como revestimento protetor em aços, eles atuam como ânodo que fornece eletrões ao aço, se começar a correr num ambiente húmido. Isto é chamado proteção catódica.
Cobre, latão, níquel, crómio, estanho e prata são mais nobres do que o aço. Se estes metais nobres forem usados como revestimento protetor, eles atuam como um cátodo. Como consequência o aço pode ser atacado diretamente e pode ocorrer ferrugem mesmo sob o revestimento se a humidade entrar em contacto com o aço (ânodo) através de poros, ou danos no revestimento.
É por isso que o zinco ou ligas de zinco são os metais de revestimento mais utilizados para produtos em aço.
Passivação
A proteção contra a corrosão oferecida pelo revestimento de zinco ou ligas de zinco pode ser melhorada consideravelmente, passivando os produtos. Na forma clássica deste tratamento é uma camada cromada extremamente fina (aproximadamente 0,1 µm) que sela os poros do revestimento de zinco ou liga de zinco e liga o oxigénio ao revestimento. Esta camada contém frequentemente crómio hexavalente (Cr(VI)) e portanto, possui uma propriedade única de “auto-regeneração”. Em caso de dano mecânico, os sais de crómio hexavanentes solúveis dentro da camada de passivação irão reparar (re-passsivar) as áreas expostas. A desvantagem deste pós-tratamento é que Cr(VI) é considerado um tratamento perigoso, substância não amiga do ambiente (tóxico e cancerígeno). O seu uso na EU é limitado e o Cr (VI) foi gradualmente banido por várias legislações (ex. RoHS, ELV (ver links no final deste documento)). Detalhes acerca do revestimento podem ser encontrados na norma lSO 4520.
Dependendo da espessura e composição da passivação, a cor varia de transparente (branco), a azul, a amarelo, até preto.
Passivação branco/azul
Este é o tipo mais comum, oferecendo baixa proteção contra a corrosão, e portanto, recomendado para aplicações internas.
Passivação preto
O mesmo nível de proteção que a passivação branca/azul e principalmente escolhido pela sua cor preta. Contém Cr(VI).
Passivação amarelo
Este tipo de passivação oferece uma melhor resistência à corrosão e geralmente é aconselhável para aplicações exteriores, no entanto diminuí em popularidade, pois o conteúdo de Cr(VI) é significativo.
Passivação verde
Estes tipos de passivação são principalmente para aplicações militares. A resistência à corrosão é comparável ou ligeiramente melhor do que a passivação amarela, e também contêm Cr(VI).
Passivação com crómio trivalente (Cr(III))
Como resultado da legislação sobre substâncias perigosas, como RoHS, Reach e ELV, um novo tipo de passivação teve de ser desenvolvido. Esta nova passivação não pode conter Cr(VI). Em vez de Cr(VI), presente na passivação preta, amarela e verde, a maioria das passivações recém-desenvolvidas usam crómio trivalente (Cr(III)). Algumas destas passivações ainda possuem melhor resistência à corrosão do que a passivação com Cr(VI). Eles são frequentemente referidos como ‘passivação espessa’, Uma camada fina pode ter a espessura de 0,08 a 0,1 µm, e uma camada espessa pode medir 0,2 a 0,3 µm. A passivação transparente fina é usada correntemente. As passivações espessas são iridescentes (azulado-amarelado-esverdeado em zinco, amarelado-esverdeado em liga de zinco) e oferecem resistência à corrosão superior, melhor que a passivação amarela com Cr(VI). Para melhorar ainda mais a resistência à corrosão e/ou melhorar o aspeto do revestimento, um selante pode ser aplicado.
Disfunção hidrogénica
O processo de electro zincagem utiliza eletricidade para precipitar zinco ou ligas de zinco. A corrente causa também a eletrólise da água no banho, separando o hidrogénio e o oxigénio.
O oxigénio desaparece do líquido no banho, mas os iões de hidrogénio podem difundir-se no metal dos artigos de fixação e unir-se às moléculas de hidrogénio. Isto é acompanhado por um aumento de volume, que causa um aumento de stress na estrutura metálica. Na presença de forças de tensão externas, isto pode dar origem a fraturas tardias, espontâneas e quebradiças. Aliás, decapagem sem inibidores (decapagem como a utilizada no processo de galvanização a quente) e o processo não qualificado de tempera de aços, com altas propriedades mecânicas, também pode induzir a disfunção hidrogénica.
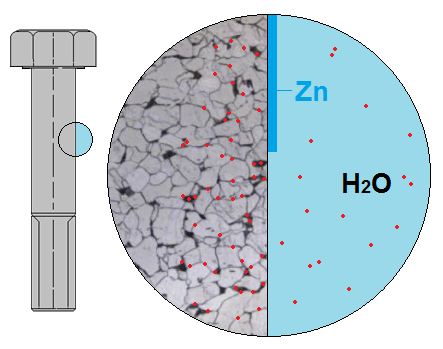

O perigo da disfunção hidrogénica aplica-se aos produtos:
- com força de tração ≥ 1000 MPa
- com dureza ≥ HV320
- com endurecimento
Para reduzir o risco de disfunção hidrogénica ao mínimo, estes produtos devem ser reaquecidos (recozido) após o processo de electro zincagem por certo período de tempo e a uma certa temperatura. A norma internacional para revestimentos electro zincados em artigos de fixação, ISO 4042 edição 1999, declara (entre outras coisas) que peças electro zincadas devem ser recozidas dentro de 4 horas, mas de preferência dentro de uma hora após a electro zincagem e antes da passivação, a uma temperatura parcial de 200°C a 230°C. A temperatura máxima deve levar em consideração o material de revestimento e o tipo de material base.
Com o aumento da espessura do revestimento, a dificuldade de remover o hidrogénio aumenta. A introdução de um processo de recozimento intermediário quando o revestimento é apenas de 2 µm a 5 µm pode reduzir o risco de disfunção hidrogénica.
A norma ISO 4042 não fornece as condições de recozimento exatas. Oito horas são consideradas um exemplo típico de duração de recozimento. No entanto, as durações de cozedura na faixa de 2h a 24h a 200°C a 230°C podem ser adequadas de acordo com o tipo e o tamanho das peças, geometria, propriedades mecânicas, processos de limpeza e processos de electro zincagem usados.
Para componentes críticos, recomenda-se que a temperatura e o tempo sejam estabelecidos experimentalmente, no entanto, a temperatura do reaquecimento nunca deve exceder a temperatura da tempera. O tempo de reaquecimento começa assim que os produtos atinjam a temperatura mínima.
Apesar de todos os cuidados, os atuais processos de electro zincagem podem reduzir o perigo da disfunção hidrogénica, mas não se pode eliminar completamente. Se para aplicações criticas, em que não pode existir nenhum risco, outro método de revestimento deve ser escolhido (ex. revestimentos zinc flake).
Sistema de codificação para electro zincagem
De acordo com o ISO 4042:1999 os revestimentos electro zincados são designados por um código composto por duas letras maiúsculas e um número. Um novo sistema de codificação está sendo preparado para a próxima edição da ISO 4042.
O código atual é construído da seguinte forma:
- Uma letra maiúscula para o revestimento de metal, ver tabela 1
- Um número para a espessura mínima de revestimento (estrutura de revestimento), ver tabela 2
- Uma letra maiúscula para o grau de brilho e tratamento, ver tabela 3
Tabela 1 baseada na ISO 4042:1999
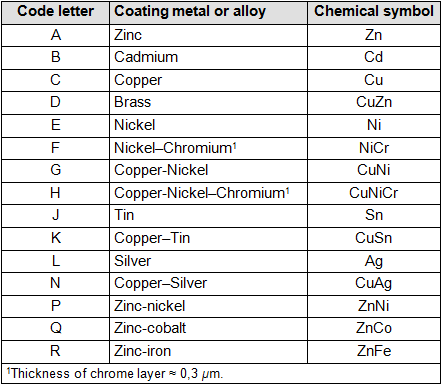
Tabela 2 baseada na ISO 4042:1999
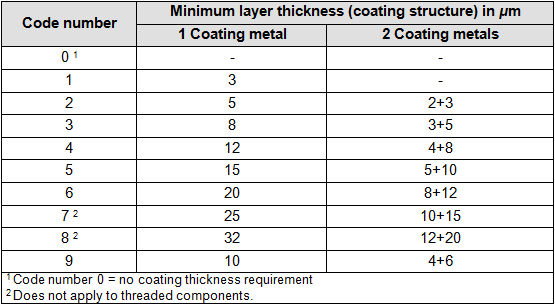
Tabela 3 baseada na ISO 4042:1999
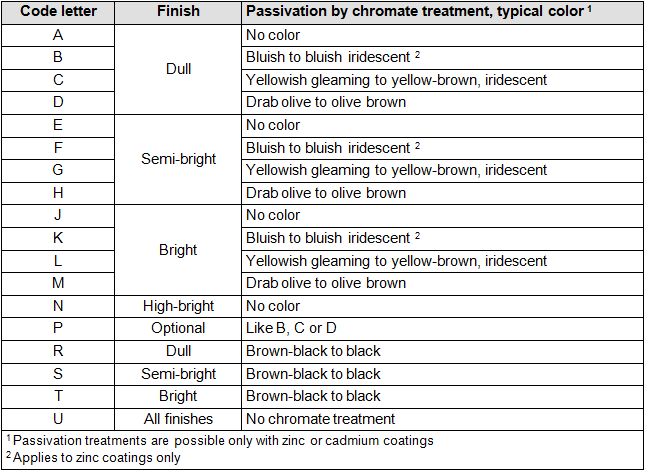
Exemplo de codificação: A3L
“A” significa zincado (ver tabela 1)
“3” indica a espessura de revestimento de pelo menos 8 microns (ver tabela 2)
“L” refere uma passivação de amarelo brilhante (ver tabela 3)
Exemplo de designação: parafuso sextavado DIN 931 – M16 x 60 – 8.8 – A3L.
Se nenhuma espessura de revestimento for acordada, a espessura de revestimento disponível comercialmente, é fornecida.
Restrições da espessura de revestimento
O grau de proteção contra a corrosão é geralmente proporcional à espessura do revestimento aplicado. No entanto, com revestimentos electro zincados em artigos de fixação, a espessura não é distribuída igualmente (é, entre outras coisas, dependente da relação entre comprimento e diâmetro l/d). Para a proteção de um artigo, a espessura mínima da camada de revestimento é normativa. Para evitar que a porca/parafuso gripem durante a montagem, a espessura nominal máxima de revestimento não deve exceder 1/4 da tolerância (ver figura abaixo).

No triângulo em ângulo reto ABC, AB é a espessura do revestimento. O aumento do diâmetro do passo devido à camada de revestimento é:

A tabela 4 mostra a espessura máxima de revestimento permitida para artigos de fixação com rosca externa com a posição de tolerância g (antes do revestimento), em relação ao passo de rosca e ao comprimento nominal.

Localização do teste de espessura da camada
A espessura mínima de revestimento nos artigos de fixação deve ser medida nos pontos indicados na figura abaixo.
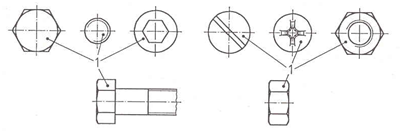
A espessura média da camada de revestimento de um lote deve ser determinada usando o método descrito na norma ISO 4042, anexo D. Salvo acordo em contrário, a espessura da camada de revestimento deve ser medida.