GALVANICKÉ ZINKOVÁNÍ NEBO POVLAKOVÁNÍ SLITINOU ZINKU
Jde o zdaleka nejběžněji používanou povrchovou úpravu ocelových spojovacích součástí. Při elektrolytickém (galvanickém) procesu se na povrchu spojovací součásti usazuje velmi tenká vrstva (3 až 20 mikronů* u závitových spojovacích součástí) zinku nebo slitiny zinku (např. ZnFe, ZnNi). Bezprostředně po potažení výrobků vrstvou zinku je vrstva zinku nebo zinkové slitiny opatřena další pasivační ochrannou vrstvou. Existuje mnoho různých druhů pasivačních vrstev, každý s různou barvou a ochrannými aspekty, takže v nabídce jsou různé spojovací součásti elektrolyticky potažené vrstvou zinku nebo zinkové slitiny.
*Jeden mikron neboli μm je
POSTUP ELEKTROLYTICKÉHO POZINKOVÁNÍ

Jak znázorňuje výše uvedený obrázek, spojovací součásti určené k pozinkování jsou vloženy do otočného plastového bubnu, ponořeny do nádrže naplněné elektrolytem (vodivou tekutinou) a do ní je přiveden záporný náboj (katoda). V nádrži jsou umístěny tyče nebo plechy ze zinku nebo zinkové slitiny s kladným nábojem (anoda). Elektrický proud přenáší ionty zinku nebo zinkové slitiny na ocelové spojovací součásti se záporným nábojem.
Zinek a slitiny zinku jsou méně ušlechtilé než ocel. Pokud jsou použity jako ochranný povlak oceli, fungují jako anoda, která dodává elektrony oceli, když začne ve vlhkém prostředí korodovat. Tento jev se nazývá katodová ochrana.
Měď, mosaz, nikl, chrom, cín a stříbro je ušlechtilejší než ocel. Pokud jsou tyto ušlechtilé kovy použity jako ochranný povlak oceli, fungují jako katoda. V důsledku toho může dojít k přímému zasažení oceli a rez se může objevit dokonce i pod ochranným povlakem, pokud vlhkost přijde do kontaktu s ocelí (anodou) skrz póry nebo poškození povlaku.
Právě proto se k povlakování ocelových výrobků používá nejčastěji zinek nebo jeho slitiny.
PASIVACE (CHROMÁTOVÁNÍ)
Ochranu proti korozi zajišťovanou povlakem zinku nebo zinkové slitiny lze významně zlepšit pasivací. V klasické formě této následné povrchové úpravy se vytvoří extrémně tenká vrstva chrómu (přibližně 0,1 µm). Tato vrstva uzavře póry ve vrstvě zinku nebo zinkové slitiny a také váže kyslík. Často obsahuje šestimocný chrom, Cr(VI), a vyznačuje se tedy jedinečnou vlastností „automatických oprav“. V případě mechanického poškození rozpustné soli šestimocného chrómu v pasivační vrstvě opraví (znovu pasivují) obnažená místa. Stinnou stránkou této následné povrchové úpravy je, že Cr(VI) je považován za nebezpečnou látku škodlivou pro životní prostředí, protože je toxický a karcinogenní. Jeho použití v zemích EU je regulováno a postupně je zakazován různými zákonnými předpisy (např. RoHS, ELV). Podrobné informace o chromových povlacích naleznete v mezinárodní normě lSO 4520.
V závislosti na tloušťce a složení pasivační vrstvy se barva pohybuje od průhledné (bílé) až po modrou a od žluté až po černou.
BÍLÁ NEBO MODRÁ PASIVACE
Tento typ následné úpravy spojovacích součástí je nejběžnější. Nabízí nízkou úroveň ochrany proti korozi a proto je doporučen pro aplikaci v interiérech.
ČERNÁ PASIVACE
Černá pasivace poskytuje stejnou úroveň ochrany jako pasivace bílá nebo modrá a obvykle se volí kvůli své černé barvě. Obsahuje Cr(VI).
ŽLUTÁ PASIVACE
Tento typ pasivace zajišťuje daleko lepší ochranu proti korozi a je běžně doporučován k venkovnímu použití; jeho popularita však nadále klesá, protože obsahuje značné množství Cr(VI).
(OLIVOVÁ) ZELENÁ PASIVACE
Tyto typy pasivace jsou určeny hlavně pro vojenské použití. Protikorozní odolnost obou typů je srovnatelná nebo poněkud lepší než u žluté pasivace a oba také obsahují Cr(VI).
PASIVACE TROJMOCNÝM CHRÓMEM CR(III)
VODÍKOVÉ KŘEHNUTÍ
Tento proces galvanického povlakování využívá elektřinu ke srážení zinku nebo jeho slitin. Elektrický proud také způsobuje částečnou hydrolýzu vody v lázni na vodík a kyslík.
Kyslík z lázně unikne, ale ionty vodíku mohou prolnout do kovu spojovacích součástí a navázat se na molekuly vodíku. Tento proces je provázen zvýšením objemu, což způsobuje vysoké napětí struktury kovu. Při působení vnějších sil v tahu může takové napětí vést ke zpožděnému a spontánnímu křehkému lomu. Vodíkové křehnutí může být vyvoláno i mořením (které se používá při procesu žárového zinkování) bez inhibitorů a neodborným kalením a popouštěním ocelí s vysokými mechanickými vlastnostmi.
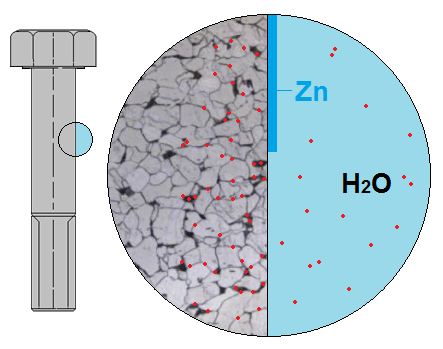

Nebezpečí vodíkového křehnutí se týká výrobků s několika charakteristikami:
- pevnost v tahu ≥ 1000 MPa
- tvrdost ≥ HV320,
- které jsou povrchově tvrzené
K minimalizaci rizika vodíkového křehnutí je nutné tyto výrobky následně po procesu galvanického povlakování znovu ohřívat (vypalovat) po určitou dobu a při stanovené teplotě. Mezinárodní norma pro galvanické povlakování spojovacích součástí ISO 4042, vydání 1999, uvádí, že galvanicky povlakované díly je nutné vypalovat při teplotě 200°C až 230°C do čtyř hodin po ukončení galvanického povlakování, nejlépe však do jedné hodiny, a před chromátováním. Maximální teplota musí být stanovena podle povlakového materiálu a typu podkladu.
S narůstající tloušťkou povlaku se zvyšuje obtížnost odstraňování vodíku. Nicméně zavedení předběžného vypalování po dosažení tloušťky povlaku 2 µm až 5 µm může snížit riziko vodíkového křehnutí.
ISO 4042 nestanoví přesné podmínky pro vypalování. Osm hodin je považováno za typickou dobu vypalování. V závislosti na typu součásti, velikosti, geometrii a mechanických vlastnostech a použitých procesech čištění a galvanického pokovování se však doba vypalování může pohybovat v rozmezí od 2 hodin do 24 hodin při teplotě mezi 200 a 230 °C.
U kritických součástí se doporučuje stanovit teplotu a dobu vypalování experimentálně, ale důležité je aby teplota vypalování nikdy nepřekročila teplotu popouštění. Doba vypalování začíná, jakmile výrobky dosáhnou minimální vypalovací teploty.
Navzdory veškeré péči věnované těmto procesům mohou metody galvanického povlakování pouze snížit riziko vodíkového křehnutí, ale nemohou je odstranit úplně. U kritických použití, kde je toto riziko nepřijatelné, musí být zvolena jiná metoda povlakování (např. povlakování vločkovým zinkem).
KÓDOVÝ SYSTÉM PRO OBJEDNÁVÁNÍ GALVANICKÉHO POZINKOVÁNÍ
Podle ISO 4042:1999 jsou galvanické povlaky mechanických spojovacích součástí označeny kódem, který se skládá ze dvou velkých písmen a čísla. Pro nové vydání ISO 4042 je připravován nový systém kódů.
Současný kód má následující strukturu:
- Jedno velké písmeno označující povlakový kov; viz Tabulka 1
- Jedno velké písmeno označující povlakový kov; viz Tabulka 1
- Jedno velké písmeno označující stupeň lesku a následnou úpravu, viz Tabulka 3
Všechny tyto tabulky jsou založeny na ISO 4042:1999
TABULKA 1
Kódové písmeno | Povlakový kov nebo slitina | Chemická značka |
A | Zinek | Zn |
B | Kadmium | Cd |
C | Měď | Cu |
D | Mosaz | CuZn |
E | Nikl | Ni |
F | Chrom-nikl1 | NiCr |
G | Měď-Nikl | CuNi |
H | Měď-Nikl-Chrom1 | CuNiCr |
J | Cín | Sn |
K | Měď-Cín | CuSn |
L | Stříbro | Ag |
N | Měď-Stříbro | CuAg |
P | Zinek-nikl | ZnNi |
Q | Zinek-kobalt | ZnCo |
R | Zinek-železo | ZnFe |
1Tloušťka vrstvy chrómu * 0,3 μm. |
TABULKA 2
Kódové číslo | Minimální tloušťka vrstvy (struktura povlaku) v μm | |
1 Povlakový kov | 2 Povlakové kovy | |
01 | - | - |
1 | 3 | - |
2 | 5 | 2+3 |
3 | 8 | 3+5 |
4 | 12 | 4+8 |
5 | 15 | 5+10 |
6 | 20 | 8+12 |
72 | 25 | 10+15 |
82 | 32 | 12+20 |
9 | 10 | 4+6 |
1 Kódové číslo 0 = žádný požadavek na tloušťku povlaku 2 Nevztahuje se na závitové součásti. |
TABULKA 3
Kódové písmeno | Konečná úprava | Pasivace chromátováním, typická barva 1 |
A | Matná | Bez barvy |
B | Měňavá modravá 2 | |
C | Lesklá žlutavá až žlutohnědá, měňavá | |
D | Olivově žlutá až olivově hnědá | |
E | Pololesklá | Bez barvy |
F | Měňavá modravá 2 | |
G | Lesklá žlutavá až žlutohnědá, měňavá | |
H | Olivově žlutá až olivově hnědá | |
J | Lesklá | Bez barvy |
K | Měňavá modravá 2 | |
L | Lesklá žlutavá až žlutohnědá, měňavá | |
M | Olivově žlutá až olivově hnědá | |
N | Vysoký lesk | Bez barvy |
P | Volitelná | JakoB, KorD |
R | Matná | Hnědočerná až černá |
S | Pololesklá | Hnědočerná až černá |
T | Lesklá | Hnědočerná až černá |
U | Všechny typy konečné úpravy | Následná úprava bez chrómu |
1 Pasivační úpravy jsou možné pouze u zinkových nebo kadmiových povlaků 2 Vztahuje se pouze na zinkové povlaky |
Příklad kódového označení: A3L
„A“ znamená pozinkování; viz Tabulka 1
„3“ znamená tloušťku vrstvy alespoň 8 mikronů; viz Tabulka 2
„L“ znamená lesklou žlutou pasivaci; viz Tabulka 3
Příklad označení: šroub s šestihrannou hlavou DIN 931 – M16 x 60 – 8.8 – A3L.
Pokud není dohodnuta žádná tloušťka povlaku, je dodána komerčně dostupná tloušťka povlaku.
OMEZENÍ TLOUŠŤKY POVLAKU
Míra ochrany proti korozi obecně závisí na tloušťce aplikované vrstvy. U galvanických povlaků na spojovacích součástech však není tloušťka rovnoměrná; závisí mimo jiné na poměru mezi délkou a průměrem l/d. Pro ochranu dílu je rozhodující minimální lokální tloušťka vrstvy. Aby nedocházelo k zadrhávání matice nebo šroubu při montáži, nesmí maximální jmenovitá tloušťka vrstvy překročit 1/4 povolené odchylky (viz obrázek níže).

V pravoúhlém trojúhelníku ABC, představuje strana AB tloušťku vrstvy. Zvýšení průměru v důsledku aplikace vrstvy povlaku je vyjádřeno níže uvedenou rovnicí:

Vnější závit | ||||||
Stoupání P | Jmenovitý průměr závitu d1 | Toleranční poloha g | ||||
Základní povolená odchylka | Jmenovitá maximální tloušťka vrstvy | |||||
2 | 3 | |||||
Všechny jmenovité délky | Jmenovitá délka L | |||||
L≤5d | 5d<L≤10d | 10d<L≤15d | ||||
mm | mm | μm | μm | μm | μm | μm |
0,2 |
| -17 | 3 | 3 | 3 | 3 |
0,25 | 1; 1,2 | -18 | 3 | 3 | 3 | 3 |
0,3 | 1 4 | -18 | 3 | 3 | 3 | 3 |
0,35 | 1,6(1,8) | -19 | 3 | 3 | 3 | 3 |
0,4 | 2 | -19 | 3 | 3 | 3 | 3 |
0,45 | 2,5 (2,2) | -20 | 5 | 5 | 3 | 3 |
0,5 | 3 | -20 | 5 | 5 | 3 | 3 |
0,6 | 3,5 | -21 | 5 | 5 | 3 | 3 |
0,7 | 4 | -22 | 5 | 5 | 3 | 3 |
0,75 | 4,5 | -22 | 5 | 5 | 3 | 3 |
0,8 | 5 | -24 | 5 | 5 | 3 | 3 |
1 | 6(7) | -26 | 5 | 5 | 3 | 3 |
1,25 | 8 | -28 | 5 | 5 | 5 | 3 |
1,5 | 10 | -32 | 8 | 8 | 5 | 5 |
1,75 | 12 | -34 | 8 | 8 | 5 | 5 |
2 | 16(14) | -38 | 8 | 8 | 5 | 5 |
2,5 | 20 (18; 22) | -42 | 10 | 10 | 8 | 8 |
3 | 24 (27) | -48 | 12 | 12 | 8 | 8 |
3,5 | 30 (33) | -53 | 12 | 12 | 10 | 8 |
4 | 36(30) | -60 | 15 | 15 | 12 | 10 |
4,5 | 42 (45) | -63 | 15 | 15 | 12 | 10 |
5 | 48(52) | -71 | 15 | 15 | 12 | 10 |
5,5 | 56(60) | -75 | 15 | 15 | 15 | 12 |
6 | 64 | -80 | 20 | 20 | 15 | 12 |
1 Informace týkající se závitů s velkým stoupáním jsou pouze orientační. Určující charakteristikou je stoupání závitu. |
MÍSTO ZKOUŠENÍ TLOUŠŤKY VRSTVY
Minimální lokální tloušťka vrstvy na spojovacích součástech se měří v bodech uvedených na obrázku níže.
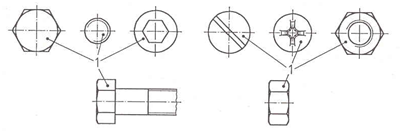
Průměrná tloušťka vrstvy v šarži musí být stanovena s využitím metody popsané v příloze D normy ISO 4042. Pokud není dohodnuto jinak, musí být lokální tloušťka vrstvy měřena.