Électro-zingage ou alliage de zinc
C'est de loin le traitement de surface le plus courant pour les fixations en acier. Une couche très mince (3 à 20 microns * pour les fixations filetées) en zinc ou en alliage de zinc (par exemple, ZnFe, ZnNi) est déposée sur la surface de la fixation par un procédé électrolytique (galvanique). Directement après que les produits ont été recouverts de zinc, une couche de passivation est ajoutée à la couche de zinc ou d'alliage de zinc qui sert à la protéger. Il existe de nombreux types de couches de passivation, chacune ayant des couleurs et des aspects de protection différents, offrant ainsi diverses pièces de fixation galvanisées en zinc ou en alliage de zinc.
* Un micron ou un µm vaut 0,001 millimètre.
LE PROCESSUS D’ÉLECTRO-ZINGAGE

Comme le montre l'image ci-dessus, les fixations à revêtir sont placées dans un tambour en plastique rotatif, immergé dans un réservoir rempli d'un électrolyte (fluide conducteur) et chargé (cathode). Des barres ou des feuilles de zinc ou d'alliage de zinc sont présentes dans le réservoir et sont chargées positivement (anode). Le courant électrique transporte les ions zinc ou alliage de zinc vers les fixations en acier chargées négativement.
Le zinc ou les alliages de zinc sont moins nobles que l'acier. Utilisés comme revêtement de protection sur l'acier, ils agissent comme une anode qui fournit des électrons à l'acier s'il commence à se corroder dans un environnement humide. Ceci s'appelle la protection cathodique.
Le cuivre, le laiton, le nickel, le chrome, l'étain et l'argent sont plus nobles que l'acier. Si ces métaux nobles sont utilisés comme revêtement protecteur, ils agissent comme une cathode. En conséquence, l’acier peut être attaqué directement, et la rouille peut apparaître même sous le revêtement si de l’humidité entre en contact avec l’acier (anode) à travers les pores ou des dommages dans le revêtement.
Cette relation est la raison pour laquelle le zinc ou les alliages de zinc sont les métaux les plus utilisés pour le revêtement des produits en acier.
PASSIVATION (CHROMATATION)
La protection contre la corrosion offerte par les couches de zinc ou d'alliage de zinc peut être considérablement améliorée en passivant les produits. Sous la forme classique de ce traitement de suivi, une couche de chromate extrêmement mince (environ 0,1 µm) est formée. Cette couche scelle les pores de la couche de zinc ou d'alliage de zinc et y lie également l'oxygène. Il contient souvent du chrome hexavalent, Cr (VI), et possède donc une propriété unique d'auto-guérison. En cas de dommage mécanique, les sels de chrome hexavalent solubles dans la couche de passivation réparent (re-passiver) les zones exposées. L'inconvénient de ce post-traitement est que le Cr (VI) est considéré comme une substance dangereuse et nuisible à l'environnement car il est toxique et cancérigène. Son utilisation dans l'UE est limitée et le Cr (VI) a été progressivement interdit par diverses législations (par exemple, RoHS, ELV). Des détails sur les revêtements de conversion de chromate peuvent être trouvés dans la norme internationale ISO 4520.
En fonction de l'épaisseur et de la composition de la couche de passivation, la couleur varie du transparent (blanc) au bleu et du jaune au noir.
PASSIVATION BLANCHE OU BLEUE
C’est la plus courante pour les fixations. Elle offre une faible protection contre la corrosion et est donc conseillé pour les applications en intérieur.
PASSIVATION NOIRE
La passivation noire offre le même niveau de protection que la passivation blanche ou bleue et est généralement choisie pour sa couleur noire. Il contient Cr (VI).
PASSIVATION JAUNE
Ce type de passivation offre une meilleure résistance à la corrosion et est généralement conseillé pour les applications en extérieur. Cependant, sa popularité continue de diminuer car le contenu en Cr (VI) est important.
(OLIVE) PASSIVATION VERTE
Ces types de passivation sont principalement destinés à des applications militaires. La résistance à la corrosion des deux types est comparable ou légèrement supérieure à la passivation jaune, et ils contiennent également du Cr (VI).
PASSIVATION CHROME TRIVALENT CR (III)
En conséquence de la législation sur les substances dangereuses, comme RoHS, Reach et ELV, un nouveau type de couche de passivation sans Cr (VI) a dû être développé. Au lieu de Cr (VI), présent dans les couches de passivation (chromate) noires, jaunes, brunes et vertes, la plupart des couches de passivation récemment développées utilisent du chrome trivalent, abrégé Cr (III). Certains de ces types de passivation possèdent même une meilleure résistance à la corrosion que la passivation au Cr (VI). On les appelle souvent «passivation à couche épaisse». Une couche mince peut mesurer de 0,08 à 0,1 µm, tandis qu'une couche épaisse est d'environ 0,2 à 0,3 µm. La passivation transparente en couche mince est la plus couramment utilisée. La passivation en couche épaisse est souvent irisée (bleuâtre-jaunâtre-verdâtre sur les couches de zinc et jaunâtre-verdâtre sur les couches d'alliage de zinc) et offre une résistance supérieure à la corrosion, meilleure que la passivation jaune Cr (VI). Pour améliorer encore la résistance à la corrosion et / ou améliorer l'aspect du revêtement, un produit d'étanchéité peut être appliqué.
FRAGILISATION PAR L'HYDROGENE
Le procédé de galvanoplastie utilise de l'électricité pour précipiter le zinc ou les alliages de zinc. Le courant provoque également l'électrolyse partielle de l'eau dans l'hydrogène et l'oxygène dans le bain.
L'oxygène disparaît du liquide dans le bain, mais les ions hydrogène peuvent diffuser dans le métal des fixations et se lier aux molécules d'hydrogène. Ce processus s'accompagne d'une augmentation de volume, ce qui provoque des contraintes importantes dans la structure métallique. En présence de forces de traction externes, ces contraintes peuvent provoquer des fractures fragiles retardées et spontanées. Incidemment, la fragilisation par l'hydrogène peut également être induite par le décapage (qui est utilisé dans le procédé de galvanisation à chaud) sans inhibiteurs et la trempe et le revenu non qualifiés des aciers à hautes propriétés mécaniques.
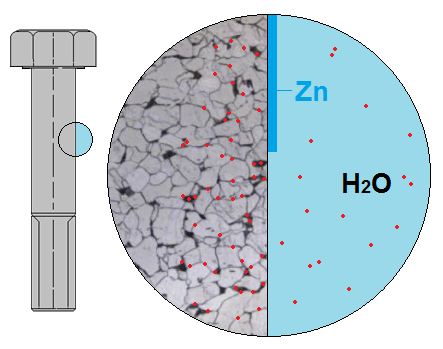

Le risque de fragilisation par l'hydrogène s'applique aux produits présentant plusieurs caractéristiques:
- Une résistance à la traction ≥ 1000 MPa
- Une dureté ≥ HV320
- Qui sont trempés
Pour minimiser le risque de fragilisation par l'hydrogène, ces produits doivent être réchauffés après le processus de galvanisation pendant un certain temps et à une certaine température. La norme internationale pour les revêtements électrolytiques sur les éléments de fixation, ISO 4042 édition 1999, stipule que les pièces galvanisées doivent être cuites à une température comprise entre 200 ° C et 230 ° C dans les quatre heures qui suivent la galvanisation. La température maximale doit être déterminée en tenant compte du matériau de revêtement et du type de matériau de base.
Avec l'augmentation de l'épaisseur du revêtement, la difficulté d'éliminer l'hydrogène augmente. Cependant, l'introduction d'un processus de cuisson intermédiaire lorsque le revêtement n'a que 2 à 5 µm d'épaisseur peut réduire le risque de fragilisation par l'hydrogène.
L'ISO 4042 ne fournit pas de conditions de cuisson exactes. Huit heures sont considérées comme un exemple typique de la durée de cuisson. Cependant, des durées de cuisson comprises entre 2 heures et 24 heures entre 200 ° C et 230 ° C peuvent convenir en fonction du type, de la taille, de la géométrie et des propriétés mécaniques de la pièce, ainsi que des procédés de nettoyage et de galvanoplastie utilisés.
Pour les composants critiques, il est recommandé que la température et le temps soient établis expérimentalement, mais il est important que la température de réchauffage ne dépasse jamais la température de revenu. Le temps de réchauffage commence dès que les produits ont atteint la température minimale.
Malgré tous les soins apportés aux procédés, les techniques actuelles de galvanoplastie ne peuvent que réduire le risque de fragilisation par l’hydrogène et non l’éliminer complètement. Pour les applications critiques dans lesquelles le risque est inacceptable, une autre méthode de revêtement doit être choisie (par exemple, des revêtements en zinc lamellaire).
SYSTÈME DE CODE POUR L’ELECTROZINGAGE
Selon la norme ISO 4042: 1999, les revêtements électrolytiques des fixations mécaniques sont désignés par un code composé de deux lettres majuscules et d’un chiffre. Un nouveau système de codage est en préparation pour la prochaine édition, ISO 4042.
Le code actuel est structuré comme suit:
- Lettre de code pour le métal de revêtement; voir table 1
- Numéro de code pour l’épaisseur minimale de couche; voir table 2
- Lettre de code pour le type de passivation utilisée sur le revêtement métallique; voir table 3
Toutes les tables sont basées sur la norme ISO 4042: 1999
TABLE 1
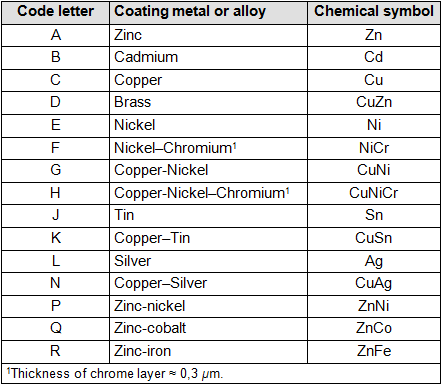
TABLE 2
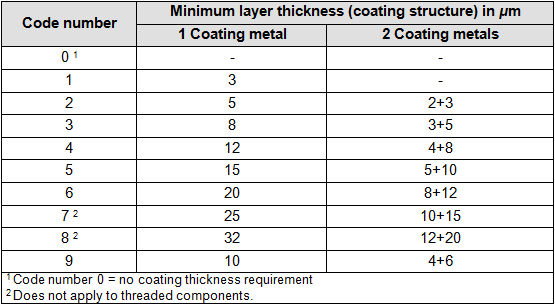
TABLE 3
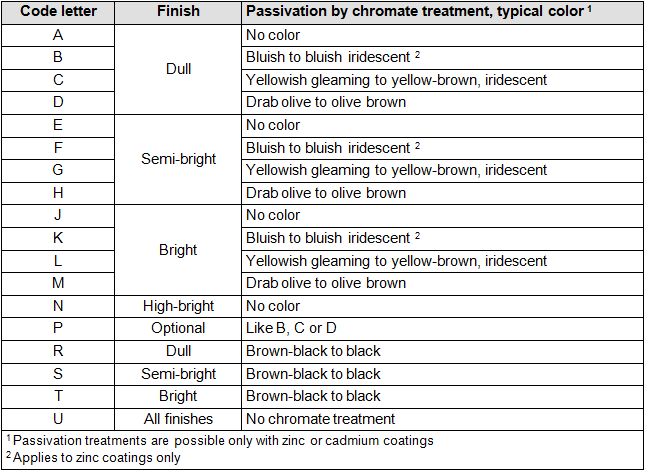
Exemple de codage: A3L
"A" signifie zingage; voir table 1
"3" Indique l'épaisseur de la couche d'au moins 8 microns; voir table 2
"L" désigne la chromatation jaune avec un degré de brillance égal à ''brillant''; voir table 3
Exemple de désignation: vis à tête hexagonale DIN 931 - M16 x 60 - 8,8 - A3L.
Si aucune épaisseur de revêtement n'est convenue, l'épaisseur de revêtement par défaut sera fournie.
LIMITES D’EPAISSEUR DE REVETEMENT
Le niveau de protection contre la corrosion est généralement proportionnel à l’épaisseur du revêtement appliqué. Pour les fixations filetées, l’épaisseur maximale de la couche pouvant être appliquée dépend de la différence entre le diamètre maximal du filetage extérieur et le diamètre minimal du filetage intérieur. Afin d’éviter que le filetage de l’écrou/du boulon ne se grippe pendant le montage, l’épaisseur nominale maximale de la couche ne doit pas dépasser ¼ de cette différence (voir la figure ci-dessous).

Dans le triangle rectangle ABC, AB est l'épaisseur de la couche. L'augmentation du diamètre du pas due à la couche de revêtement est désignée par la formule ci-dessous:

La table 4 indique les épaisseurs de couche maximales admissibles pour les fixations à filetage extérieur avec la position de tolérance g (avant revêtement) par rapport au pas du filet et à la longueur nominale.

EMPLACEMENT POUR ESSAIS D'ÉPAISSEUR DE LA COUCHE
L'épaisseur minimale de la couche locale sur les fixations est mesurée aux points indiqués dans la figure ci-dessous.
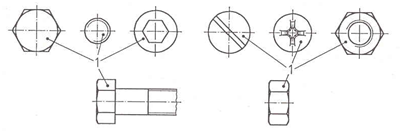
L'épaisseur de couche moyenne d'un lot doit être déterminée en utilisant la méthode décrite dans l'ISO 4042, annexe D. Sauf accord contraire, l'épaisseur de couche locale doit être mesurée.