ELEKTROLYTISCH VERZINKTE ODER ZINKLEGIERUNGSBESCHICHTUNG
Dies ist mit Abstand die gängigste Oberflächenbeschichtung für Verbindungselemente aus Stahl. Eine sehr dünne (3 bis 20 Mikrometer* für Schraubverbindungen) Zink- oder Zinklegierungsschicht (d.b. ZnFe, ZnNi) wird mithilfe eines elektrolytischen (galvanischen) Prozesses auf die Oberfläche des Verbindungselements aufgetragen. Direkt nachdem die Produkte mit dem Zink überzogen wurden, wird die Zink- oder Zinklegierungsschicht mit einer Passivierungsschicht ergänzt, die als Schutzschicht für das Zink oder die Zinklegierung dient.
Es gibt viele verschiedene Typen Passivierungsschichten mit unterschiedlichen Farben und Schutzmerkmalen, die vielseitige elektrolytische zink- oder zinklegierungsbeschichtete Verbindungselemente ermöglichen.
*Ein Mikrometer oder μm entspricht 0,001 Millimeter.
Der elektrolytische Zinkbeschichtungsprozess

Wie in der oben stehenden Abbildung dargestellt, werden die zu beschichtenden Verbindungselemente in eine rotierende Kunststofftrommel gegeben, in einen mit einem Elektrolyt (leitende Flüssigkeit) gefüllten und negativ geladenen (Kathode) Tank getaucht. Im Tank befinden sich positiv geladene Zink oder Zinklegierungs-Stangen oder -Platten (Anoden) und der elektrische Strom transportiert Zink- oder Zinklegierungsionen zu den negativ geladenen Stahl-Verbindungselementen.
Zink- oder Zinklegierungen sind weniger edel als Stahl. Bei der Verwendung als Schutzbeschichtung auf Stahl fungieren sie als Anode, die Elektronen zum Stahl befördert, wenn in einer feuchten Umgebung Korrosion auftritt. Dies ist der so genannte kathodische Schutz.
Kupfer, Messing, Nickel, Chrom, Zinn und Silber sind edler als Stahl. Wenn diese Edelmetalle als Schutzbeschichtung verwendet werden, fungieren sie als Kathode. Infolgedessen kann Stahl direkt angegriffen werden und auch unter der Beschichtung Rost entstehen, wenn Feuchtigkeit über Poren in - oder Schäden an - der Beschichtung in Kontakt mit Stahl (Anode) kommt.
Aus diesem Grund sind Zink oder Zinklegierungen die am häufigsten genutzten Beschichtungsmetalle für Stahlprodukte.
Passivierung (Chromatierung)
Der durch die Zink- oder Zinklegierungsschicht gebotene Schutz kann durch Passivierung des Produkts erheblich verbessert werden. Bei der klassischen Form dieser Nachbehandlung wird eine extrem dünne (ca. 0,1 µm) Chromatschicht gebildet, die die Poren in der Zink- oder Zinklegierungsschicht verschließt und zudem Sauerstoff daran bindet. Diese Schicht enthält häufig sechswertiges Chrom (Cr(VI)) und verfügt daher über eine einzigartige „Selbstheilungs“-Eigenschaft. Im Falle einer mechanischen Beschädigung „reparieren“ (re-passivieren) die löslichen sechswertigen Chromsalze innerhalb der Passivierungsschicht die belasteten Bereiche. Der Nachteil dieser Nachbehandlung ist, dass Cr(VI) als ein gefährlicher, umweltschädlicher Stoff (toxisch und karzinogen) betrachtet wird. Seine Anwendung ist in der EU beschränkt und CR(VI) unterliegt verschiedenen Vorschriften (z. B. RoHS, ELV (siehe Links am Ende dieses Dokuments)). Details zu Chromatbeschichtungen sind in der internationalen Norm ISO 4520 zu finden.
Je nach Dicke und Zusammensetzung der Passivierungsschicht variiert die Farbe von transparent (weiß) über blau und gelb bis zu schwarz.
Weiße/Blaue Passivierung
Dies ist der häufigste Typ für Verbindungselemente, der einen geringen Korrosionsschutz bietet und daher für Innen-Anwendungen zu empfehlen ist.
Schwarze Passivierung
Dieser Typ hat den gleichen Schutzgrad wie die weiße/blaue Passivierung und wird meistens aufgrund seiner schwarzen Farbe verwendet. Enthält Cr(VI).
Gelbe Passivierung
Dieser Passivierungstyp bietet eine weitaus besseren Korrosionswiderstand und wird in der Regel für Außenanwendungen empfohlen, auch wenn seine Popularität aufgrund des hohen Cr(VI)-Werts abnimmt.
(Oliv-) Grüne Passivierung
Diese Passivierungstypen werden insbesondere für Militäranwendungen eingesetzt. Der Korrosionswiderstand beider Typen ist vergleichbar mit bzw. leicht besser als bei der gelben Passivierung und sie enthalten ebenfalls Cr(VI).
Trivalente Chrom (CR(III))-Passivierung
Als Ergebnis der Gefahrenstoffvorschriften wie RoHS, Reach und ELV musste ein neuer Passivierungsschichttyp entwickelt werden. Diese neue Passivierungsschicht durfte kein Cr(VI) mehr enthalten. Anstatt des in der schwarzen, gelben, braunen und grünen (chromatierten) Passivierungsschichten Cr(VI) verwenden die meisten neu entwickelten Passivierungen trivalentes Chrom (Cr(III)). Einige dieser Passivierungen verfügen sogar über einen besseren Korrosionswiderstand als die Cr(VI)-Passivierung. Sie werden häufig als „Dickschichtpassivierung“ bezeichnet. Eine dünne Schicht kann zwischen 0,08 und 0,1 µm „dick“ sein und eine dicke Schicht zwischen 0,2 und 0,3 µm. Am häufigsten wird die transparente Dünnschichtpassivierung verwendet. Dickschichtpassivierungen sind irisierend (bläulich-gelblich-grünlich) und bieten einen erstklassigen Korrosionswiderstand, besser als die gelbe CR(VI)-Passivierung. Zur weiteren Optimierung des Korrosionswiderstands und/oder zur optischen Verschönerung kann ein Dichtmittel angewendet werden.
Wasserstoffversprödung
Beim elektrolytischen Beschichtungsprozess wird Elektrizität verwendet, um Zink oder Zink abzuscheiden. Der Strom bewirkt zudem die Elektrolyse des Wassers in der Wanne in Wasserstoff und Sauerstoff.
Der Sauerstoff verschwindet aus der Flüssigkeit in der Wanne, aber die Wasserstoffionen können in das Metall der Verbindungselemente diffundieren und sich zu Wasserstoffmolekülen verbinden. Dies geht mit einer Volumenzunahme einher, die eine starke Dehnung innerhalb der Metallstruktur verursacht. Bei externen Zugkräften kann dies zu verzögerten, spontanen, brüchigen Rissen führen. Gelegentlich können auch das Beizen ohne Inhibitoren (Beizen wie es beim Feuerverzinkungsprozess angewandt wird) und das unqualifizierte Abschrecken und Temperieren von Stahl mit hohen mechanischen Eigenschaften eine Wasserstoffversprödung einleiten.
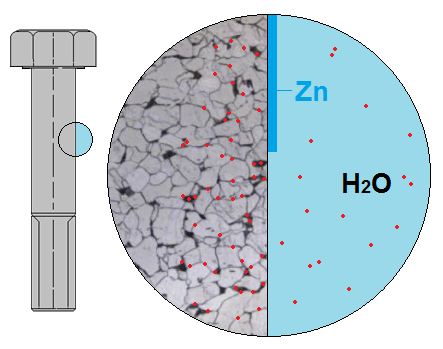

Die Gefahr der Wasserstoffversprödung betrifft Produkte:
- mit einer Zugfestigkeit ≥ 1000 MPa
- mit einer Härte ≥ HV320
- die einsatzgehärtet sind.
Um das Risiko der Wasserstoffversprödung auf ein Mindestmaß zu begrenzen, müssen diese Produkte nach dem elektrolytischen Beschichtungsprozess für eine bestimmte Zeit und bei einer bestimmten Temperatur erhitzt (gebrannt) werden. Die internationale Norm für galvanische Überzüge von Verbindungsmitteln, ISO 4042 Version 1999, legt (unter anderem) fest, dass galvanisierte Teile innerhalb von 4 Stunden gebrannt werden sollten, aber vorzugsweise innerhalb einer Stunde der Galvanisierung und vor der Chromatierung, bei einer Teiltemperatur von 200 °C bis 230 °C. Die Höchsttemperatur muss das Beschichtungsmaterial und den Typ des Basismaterials berücksichtigen.
Mit zunehmender Überzugdicke wird es schwieriger, Wasserstoff zu entfernen. Wenn der Überzug nur 2 bis 5 µm dick ist, kann die Einführung eines zwischenzeitigen Einbrennprozesses das Risiko der Wasserstoffversprödung verringern.
ISO 4042 liefert keine exakten Einbrennbedingungen. Acht Stunden wird als typische Einbrennzeit gehandhabt. Allerdings können auch Einbrennzeiten von 2 Stunden bis 24 Stunden bei 200 °C bis 230 °C geeignet sein, je nach Typ und Größe des Teils, der Teilegeometrie, der mechanischen Eigenschaften und der angewandten Reinigungs- und Galvanisierungsprozesse.
Bei kritischen Komponenten ist es zu empfehlen, die Temperatur und Zeit auszutesten, jedoch darf die Nachheiztemperatur die Anlasstemperatur niemals überschreiten. Die Nachheizzeit beginnt, sobald die Produkte die Mindesttemperatur erreicht haben.
Trotz aller Vorsichtsmaßnahmen können die Galvanisierungsprozesse das Risiko der Wasserversprödung zwar reduzieren, aber es nicht vollständig ausschalten. Wenn bei kritischen Anwendungen jedes Risiko ausgeschlossen werden muss, muss eine andere Beschichtungsmethode ausgewählt werden (z. B. Zinklamellenbeschichtungen).
Code-System für die Bestellung von elektrolytischer Zinkbeschichtung
Konform ISO 4042:1999 werden die galvanischen Überzüge mechanischer Verbindungselemente durch einen Code, bestehend aus zwei Großbuchstaben und einer Zahl festgelegt. Für die nächste ISO 4042-Version ist ein neues Kodierungssystem in Vorbereitung.
Der aktuelle Code setzt sich wie folgt zusammen:
- Ein Großbuchstabe für das Überzugmetall, siehe Tabelle 1
- Eine Zahl für die Mindestdicke der Schicht (Überzugstruktur), siehe Tabelle 2
- Ein Großbuchstabe für den Glanzgrad und die Nachbehandlung, siehe Tabelle 3
Alle tabellen sind basiert auf ISO 4042:1999
Tabelle 1
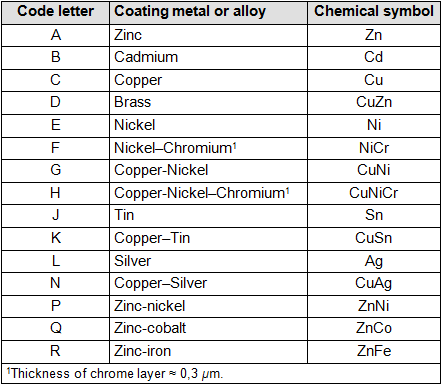
Tabelle 2
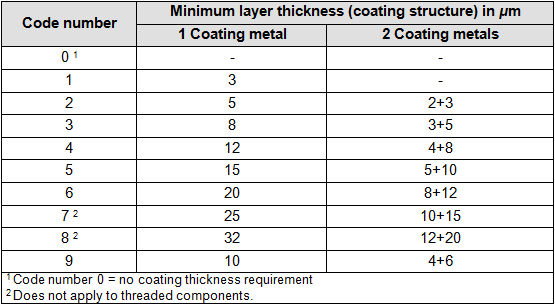
Tabelle 3
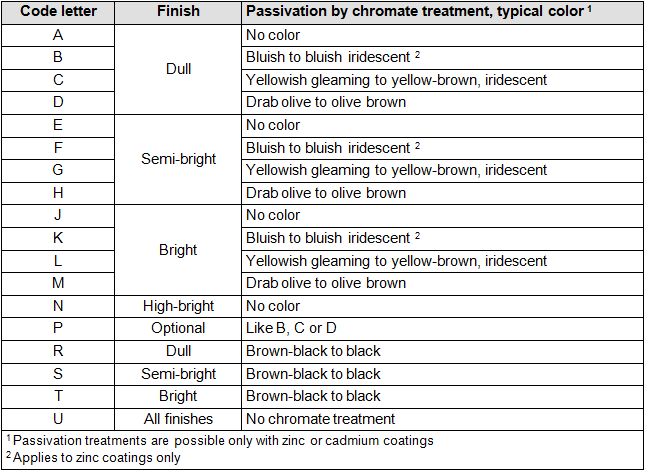
Kodierungsbeispiel: A3L
„A” bedeutet Zinkbeschichtung (siehe Tabelle 1)
„3” gibt die Schichtdicke von mindestens 8 Mikrometern an (siehe Tabelle 2)
„L” bezieht sich auf eine hellgelbe Passivierung (siehe Tabelle 3)
Zuordnungsbeispiel: Sechskantschraube DIN 931 – M16 x 60 – 8.8 – A3L.
Wenn keine Überzugsdicke vereinbart wurde, wird die handelsübliche Überzugdicke geliefert.
Schichtdickeneinschränkungen
Der Schutzgrad gegen Korrosion verhält sich grundsätzlich proportional zur Dicke der angewandten Schicht. Bei galvanischen Überzügen auf Verbindungselementen ist jedoch die Dicke nicht gleichmäßig verteilt (dies ist unter andere abhängig von der Relation zwischen Länge und Durchmesser (L/D). Für den Schutz eines Artikels ist die lokale Mindestschichtdicke maßgeblich. Um die Mutter/Schraube während der Montage vor dem Festfressen zu schützen, sollte die nominale Höchstschichtdicke 1/4 des erlaubten Werts nicht übersteigen (siehe untenstehende Abbildung).

In dem rechtwinkligen Dreieck ABC ist AB die Schichtdicke. Die Vergrößerung des Teilkreisdurchmessers aufgrund der Schichtdicke beträgt:

Tabelle 4 zeigt die maximal zulässige Schichtdicke für Verbindungselemente mit Außengewinde mit einer Toleranzposition g (vor der Beschichtung), in Relation zur Gewindesteigung und der Nennlänge.

Schichtdicke Prüfstelle
Die lokale Mindestschichtdicke an Verbindungselementen muss an den Punkten geprüft werden, die in der nachfolgenden Abbildung gekennzeichnet sind.
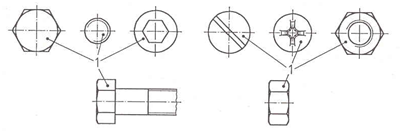
Die durchschnittliche Schichtdicke eines Batches muss mithilfe der in der ISO 4042 Anhang D beschriebenen Methode bestimmt werden. Wenn nicht anders vereinbart, muss die lokale Schichtdicke gemessen werden.