THE SEIZING EFFECT OF STAINLESS STEEL FASTENERS
INTRODUCTION
When applying stainless steel or aluminum fasteners, ‘cold welding’ (also known as seizing, galling or fretting) may occur during assembly. In this case, the threading sticks together until no further movement is possible, which may lead to the fracturing of screws during tightening. Such fracturing causes bothersome or even hazardous situations, leading to delays, damages or even injuries. If the screws do not break during assembly, they may possibly deform due to torsion or seize before the preload is correct, in which case future failures may occur due to metal fatigue or external forces on the connection. An undesirable situation is if critical connections suddenly and unexpectedly fail. If no failures occur during the lifespan of the connection, the seizing effect may cause problems during disassembly, perhaps that the fasteners just do not loosen. In the past, we have received quality concerns from customers, though investigations clarified that the cause of failure was seizing rather than product quality.
WHAT CAUSES SEIZING?
When metals move and make contact with each other, they experience friction. This friction is caused by the surface roughness of the metals, and it may result in heating and wearing of the parts. When the pressure on the contact surfaces rises, the friction also rises. For some metals, this increase in friction can lead to wear on the contact surfaces because the friction is so high that the surfaces stick together. The movement tears parts of the surface, and this effect is known as seizing, galling or fretting.
On threaded fasteners (e.g., nuts and bolts), there is a large buildup of pressure on the contact surfaces in the thread flanks, which leads to intensifying friction and adhesion, and it may lead to seizing of the threads. Products made from austenitic stainless steel or aluminum are always more sensitive to this effect in comparison to steel products, which is because since these metals are more ductile and have a crystalline atomic structure. For this reason, austenitic stainless steel fasteners present far more seizing problems than steel fasteners.
PRODUCTS AND SITUATIONS THAT MAY ENLARGE THE CHANCES OF SEIZING
Products that purposely affect higher friction in the threads (e.g., lock nuts that exert a clamping force in the threads) greatly increase the chances of seizing. This result occurs because the extra friction during movement causes significant friction energy (heat) on a very small area. These types of lock nuts do not secure the preload in the connection, but since they keep pressure on the threads after self-loosening, the nut remains on the bolt. These types of lock nuts, based on friction in the threads, do not run freely until they reach the surface of the clamped material. Every rotation of the thread produces movement, which causes friction and therefore a higher risk of seizing. Unless special lubrication measures are taken, it is advisable to use different types of locking products that operate on principles other than thread friction in order to avoid seizing problems.
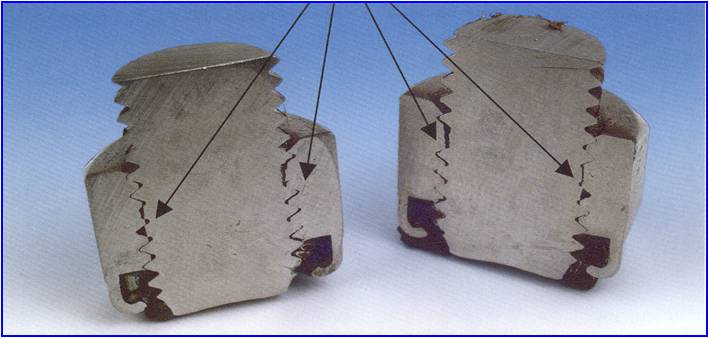
The results of seizing in a stainless steel lock nut.
Bolted connections that require high thread movement to attach, which is due to gaps in between the connecting parts, also present a higher risk of seizing. The same increased risk also applies to connections that contain ‘soft’ parts like gaskets or spring elements, such as spring washers, spring discs, coiled springs and soft washers (e.g., made from rubber or plastic). These elements also cause greater movement under friction when using threaded fasteners.

A flange connection containing a soft gasket.
Lubrinox lubricated fasteners
Fabory has developed Lubrinox specifically to prevent stainless steel from seizing. Lubrinox is the only stainless steel fastening solution with a high-end lubricating coating. Fasten stainless steel bolts and nuts faster than ever, with or without extra locking agent. This saves you time, money, energy and materials, while the quality of the connection is guaranteed. Especially when you combine a Lubrinox bolt and a Lubrinox nut.
Click here to read more about Lubrinox.
HOW TO DIMINISH SEIZING EFFECTS
It is important to always ensure that the products are clean and free from burrs, metal particles, chips, sand or dust. Moreover, local friction caused by damage to the screw threads or crooked assembly must be avoided.
Smaller axial displacement of the threads means reduced chances of seizing. Stiff connections that require only a small amount of rotation to provide preload result in a lower probability of seizing than more elastic connections that contain soft or springy elements. In the latter case, a higher axial displacement is necessary to reach the required amount of preload.
A slow and even rotation of the threaded fasteners is also advisable, and pulsing and impact tools should be avoided in order to diminish the consequences of friction in the threaded connection.
Combining two different types of austenitic stainless steel, like AISI 304 and AISI 316, is often mentioned as a way to reduce the chances of seizing. However, since both share a comparable surface roughness and atomic structure, this pairing typically does not improve the actual seizing effect. Both types have an austenitic metal structure and a high risk of seizing.
Rolled threads are favored over cut threads for the avoidance of seizing because rolling results in a lower roughness of the surface. Most of the commonly sold mass-produced stainless steel screws and bolts have rolled threads.
Products that actively reduce friction, such as lubricants with a high resistance to pressure, also often help to prevent seizing. Some lubricant manufacturers produce specific anti-seize lubricants for threaded fasteners.
Next to lubricants, which must be self-applied, there are also anti-seize coatings with lubricating properties. These can be pre-applied, and they provide a non-sticky, dry anti-friction layer. Including this layer saves assembly time, and because of the dryness of the surface layer, it is less susceptible to pollution by small particles than sticky, greasy lubricants.

CONCLUSION
By giving more attention to the assembly of stainless steel or aluminum fasteners and avoiding situations that increase friction in the threads, many problems can be prevented. Such attention increases the reliability and durability of threaded connections.